Near Miss:
Introduction:
Establish a reporting culture where every near-miss incident is accurately reported. Understand the circumstances that lead to the hazard to determine root cause. Plan and implement preventive action to immediately contain the incident. Rethink the safety process and build strategies to prevent its reoccurrence.
Definition:
OSHA defines a near miss as incidents “in which a worker might have been hurt if the circumstances had been slightly different.” They are a precursor to accidents and are opportunities to identify hazards and unsafe conditions. It goes without saying that reporting near misses is a critical tool to create solutions, prevent accidents and injuries in the future and improve your safety culture overall.
Near misses are also referred to as “close calls”, “narrow escapes” or “miss accidents”.
There are two main types of near miss incidents — unsafe condition near miss and unsafe act near miss.
Unsafe condition
Circumstances, environment, or state of equipment which could lead to an accident occurring.
Unsafe act
Behavior that can potentially lead to damage of property, personal injury, or death. It’s often related to ignoring procedures and is signaling the need for new rules.
Do you need to report near misses to OSHA?
No. You are not required to report near misses to OSHA. But they do recommend recording near miss cases.
“OSHA strongly encourages employers to investigate all incidents in which a worker was hurt, as well as close calls (sometimes called “near misses”)”
This should involve recording near misses internally and investigating each incident, regardless of the severity of harm caused.
Why is near miss reporting so important?
Simply put, without a near miss reporting software system, the learning begins only when an accident occurs and there is severe loss or injury to human life and property.
The notion of reporting close-calls when there’s no damage done seems a futile effort, especially if the odds keep falling in our favor and there are no legal obligations to do so.
Yet, history has shown that almost every catastrophic disaster is a result of overlooking near-miss warnings that preceded the event.
Accidents that are barely avoided have become commonplace in the modern workplace. With so much to do and so little time, employees often cut corners and perform unsafe activities to stay ahead. Every fortunate encounter with a near miss goes unnoticed or unreported and is often shared casually. Even reporting near-misses or following up on its progress is avoided as it takes time off the task at hand. While some avoid reporting unsafe acts by their fellow employees as it may lead to chastisement, fear of being blamed or even disciplinary action for reporting.
Writing off a near miss as “no harm no foul” can prove detrimental in the long run. At some point the chain breaks and the luck finally run out, leading to a catastrophic event that gets everyone’s undivided attention to a prevailing hazard.
Near miss reporting is the only recognized incident management structure that accurately identifies and reports near misses, effectively communicates risk tolerance measures to employees, eradicates the root cause of the hazard and prevents future accidents or injuries from taking place.
Benefits of reporting near misses
Since the same factors that lead to a near miss can lead to an accident, monitoring near misses can help you take proactive action to:
- Identify systemic health and safety issues
Identify patterns in when or how things go wrong
- Improve workplace health and safety
- Improve health and safety training
- Improve equipment and property maintenance
- Remove, reduce, or mitigate risks and hazards
- Encourage employees to comply with health and safety policies
- Enhance the safety culture
- Develop more effective health and safety policies
- Reduce the number of workplace incidents
- Save time and money for the organization
What are the causes of near misses?
Thought accidents are impervious to time and space, identifying the core root of an underlying anomaly helps us understand the origins of a hazard and form preventive actions to contain its escalation. Some of the most common causes of near misses are:
- Unsafe conditions
- Unsafe work practices
- Unsafe procedures
- Human error
- Lack of training
- Lack of safety awareness
- Employees that cut corners
- Lack of communication
- Unsafe tools
- No standardized procedure to report near misses
The Near Miss Pyramid Theory
Herbert Heinrich wrote in his 1931 book Industrial Accident Prevention, A Scientific Approach,
“No matter how strongly the statistical records emphasize personal faults or how imperatively the need for educational activity is shown, no safety procedure is complete or satisfactory that does not provide for the . . . correction or elimination of . . . physical hazards,”
He was referring to the correction of potential hazards before an accident happens. And, one of the easiest ways to do this is to look at accidents that could happen, before they do.
It was Heinrich who developed the Near Miss Pyramid Theory – a theory which states that for every single fatal incident a company experiences, it will have had 29 serious disabling workplace injuries and 300 lost time incidents.
How many near misses per accident?
In 1966, Frank Bird analyzed the incident reports of over 300 companies — 1.7 million reports in total. He used his findings to expand Heinrich’s theory. Bird’s Safety Triangle looks deeper into the behaviors leading to potential accidents. In his book, Damage Control, he determined that for each fatality, a company will see:
There have been many further studies on this subject. Heinrich and Bird’s theory is reflected in most workplaces. But the figures differ depending on the size of the workforce.
Examples of near miss reporting:
Determining what constitutes a near miss scenario is easy. Be it any industry, look for incidents or behavioral patterns in which actions that could have led to severe consequences but did not lead to its logical conclusion due to a fortunate turn of events, can be classified as a near miss. Some common near miss scenarios include:
- Non-injury caused due to falling from heights including stairs, Mobile elevated work platforms (MEWA), rooftops and more
- Slippery conditions that could have led to slips or trips that cause serious injuries or dislocations.
- Working on machinery without proper Lockout or Tagout procedures (LOTO).
- Working without proper personal protective equipment PPE like helmets, gloves, etc.
- Risky or negligent behavior in several scenarios like driving heavy machinery above the prescribed speed limit.
- Close shave caused due to improper training or maintenance of machinery.
- Evading the path of a falling object
- Near miss caused due to improper or no signage which could lead employees to enter otherwise restricted zones without isolations
key components in near miss reporting:
There is no need to set up a dedicated system for near miss reporting. You can achieve the same outcome by revising your existing safety management system criteria to include near misses. Companies that are new to a reporting culture can refer to the description of the key components in near miss reporting in the following Figure
Identify:
Employees need to understand how to properly identify and recognize near miss events. One method of training is to involve employees in job safety analysis or risk assessment that will highlight potential hazards in their work areas. This is extremely important as it will affect the
quality of the near miss reports turned in. In the earlier stages, while employees are still beginning to understand the concept of near misses, the quality of the reports may vary. But over time, you can use past reports to fine-tune their understanding or your company’s definition of a near miss event.
Report:
A complicated procedure and overly-detailed report would discourage staff. Ensure that the process for reporting near misses is hassle-free and easy to understand. The form for reporting should be kept as simple as possible. Dates, location, and general description of the near miss incident are key information to include in the form.
Investigate:
When conducting an investigation, you should not only look at what had happened, but also probe further into what could have happened. Evaluate the possible consequences of the reported near miss and rank it by its potential severity and likelihood of occurrence. This is similar to how risks are assessed in a risk matrix.
If major injuries or fatalities are likely, a full investigation is encouraged. If the potential consequences were less severe, the hazard can be easily taken care of and communicated to everyone.
Intervene:
The staff working in the area where the near miss took place should rectify the problem because they are most familiar with the worksite. Interventions can take place before and after an investigation. Encourage your employees to take action to temporarily mitigate the danger before investigations start. After completing investigations, permanent solutions can be implemented.
Review:
The data collected from near misses are leading indicators of your company’s performance. Use it together with other safety performance indicators in your evaluation. The review can be done on a daily, weekly or monthly basis to identify trends and provide solutions to remove the hazard. Reviewing and analyzing the data is an opportunity to gather feedback on performance and
enhance your workplace safety.
Difference Between Near Miss, Incident, and Accident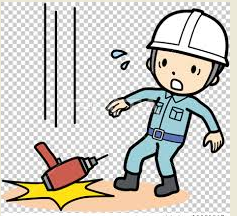
- Near miss vs. incident – Though near miss is included in the OSHA definition of incident (as an incident subtype), a key difference between them is that the worst possible outcomes of an incident, which may or may not include injury or property damage, are realized due to it not being prevented or addressed in a timely manner.
For example, if the outcome of an unsafe event is fully realized and not prevented by luck or a last-minute decision, then the unsafe event is an incident, instead of a near miss, even if it also did not result in injury or property damage.
- Near miss vs. accident – An accident is an unsafe event that results in injury or property damage. Though the OSHA definition of incident is essentially similar to accident, other safety organizations consider incident and accident to be two separate entities. A key difference between accidents and incidents (including a near miss) is that accidents are more complex, in that they do not have an apparent cause.
For example, if it is clear what caused the unsafe event to occur and its outcome includes injury or property damage, then the unsafe event is an incident, not an accident.
How to improve near miss reporting?
No-blame culture
Employees’ participation is vital for near miss reporting to succeed. Therefore, we need to educate them on why near miss reporting is necessary. Employees should also understand that they play a crucial role in the process of reporting. These must be communicated and positively reinforced to all employees across all levels.
Here are some good practices that would encourage employees to participate in near miss reporting. Reassure your employees that the information be in collected will be used to learn and improve—not to blame or punish.
To improve the quality of report submission, you can consider anonymous reporting. Employees would be more comfortable with sharing information when their identities are kept confidential. However, this could hinder information gathering during investigation when assistance from reporting employees may be needed.
It is important to earn your employees’ trust when it comes to reporting. An environment where employees feel comfortable to come forward without any fear of repercussion would make the near miss reporting system a success.
Empower employees
All employees should be empowered to spot and fix hazards at their own discretion before near misses escalate into more severe consequences. Employees usually hesitate to take action because they are unsure if it is their responsibility to do so.
Establish clear responsibilities for your employees and encourage them to cooperate and actively contribute in providing solutions.
Communication
Communication is key in promoting near miss reporting among employees. Regular and consistent communication will help to sustain the interest to report. Combining open communication with a no-blame policy will let employees feel that their suggestions are valued.
Besides highlighting the benefits of near miss reporting, communication is also about sharing near misses that employees could relate to. The sharing can be carried out by supervisors or top management to demonstrate their commitment to the well-being of their employees.
Create a culture of reporting
To establish a strong reporting culture, you should act on every opportunity to identify and control hazards, reduce risk and prevent harmful incidents. The senior management can begin by creating a policy and communicating it to all employees. The support from middle management such as managers and supervisors is vital as they work closely with the workers. Middle management managers should be role models for their subordinates and set a good example to propagate the value of near miss reporting. Besides including near miss reporting into the job scope of employees, you may also consider providing training on near miss reporting for new employees as part of their orientation.
To cultivate the habit of submitting near miss reports or collecting adequate data for analysis, you may be tempted to set quotas. Although quota-setting may help set a clearer target and expectations on a new reporting programme, it could also dilute the quality of the information you receive. If made compulsory, employees may submit reports for the sake of meeting the quota, and not out of genuine concern for safety. Employees who met their quota for that period of time may also choose to stop reporting; hence some near misses would not be identified.
Easy to understand and use
A complicated or confusing process will likely discourage employees from reporting. Therefore, it is important to ensure that the reporting process is easy to understand and implement. The form should be kept concise and questions straightforward so employees can easily learn how to use them. Lastly, obtaining the forms should also be convenient so employees can record and submit a
report readily.
Feedback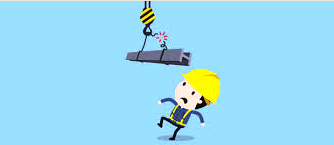
Staff should be made aware of actions that are taken in response to reported near misses. It can be shared at company meetings and project sites via platforms such as toolbox meetings. Feedback motivates employees to do near miss reporting as they can see that their suggestions are valued and help shape their workplace. In the event that more time is needed to rectify the condition, feedback will also reassure employees that their contributions are not being overlooked.
Incentives
One possible method to promote and encourage near miss reporting is to offer incentives to employees. An example of a good incentive is one that recognizes the participation of employees in the recognition and reporting of hazards. For instance, giving due credit to employees who had submitted reports that helped avert potentially disastrous accidents.
Acknowledging contribution from your staff helps to nurture a stronger reporting culture and better engage employees in purposeful activities.
An example of a poor incentive is one that measures performance by placing focus on statistics and setting numerical targets. This will have a negative impact on the reporting culture because the driving force behind reporting is to meet targets.
Steps for Setting Up a Successful Near Miss Program
A near miss program can be considered successful if it is integrated into or functions as the organization’s health and safety program. Isolating the near miss program from the wider organizational culture and other relevant policies may cause it to lose its effectiveness. To avoid implementing a faulty near miss program that becomes obsolete after a few months, follow the steps below:
Step #1 Ask Employees for Their Input
This can be done either formally via one-on-one interviews or informally via an online survey. In both cases, the health and safety team should ask employees the following questions:
- What are your thoughts on near miss reporting?
- What would stop you from reporting a near miss?
- What would encourage you to report a near miss?
- What do you think should be included in our near miss program?
- What would be your ideal form of participation in the near miss program?
Step #2 Perform Hazard Identification
This gives the health and safety team a general idea of what could possibly lead to a near miss. It also serves as training for conducting root cause analysis later on in the implementation of the near miss program. There are many types of hazards and some industries deal with specific types, such as chemical hazards in processing plants. The more common hazards, however, are safety hazards and ergonomic hazards.
Step #3 Perform Risk Assessment
Though risk assessment may include hazard identification, risk assessment focuses more on the possible consequences of a near miss, rather than possible causes. This step is crucial in spotting SIF potential even before a near miss occurs.
Risk Assessment Risk Matrix
By performing risk assessment before implementing the near miss program, the health and safety team gain a better understanding of the risks they should prioritize and prepare employees for.
Step #4 Have a Clear Implementation Plan
For any new policy, project, or program, the implementation phase either makes or breaks its success. Before jumping in though, it’s good to have a plan. When creating a plan for the implementation of the near miss program, the health and safety team must include representatives or leaders from different teams in the organization. This provides great insight on possible blockers to implementation and raises the credibility of the near miss program in the eyes of employees.
Tips for Successful Implementation of a Near Miss Program
Once the plan for implementation has been finalized, the health and safety team can proceed with the implementation itself. While the specific steps for implementing a successful near miss program differ for each organization, here are a few basic tips that could help.
Tip #1 Conduct Regular Toolbox Talks
Though a near miss reporting toolbox talk should be held before implementation, regular toolbox talks after implementation may be necessary to ensure that employees fully understand the near miss program. Additionally, the health and safety team can use the feedback given by employees during these toolbox talks to improve the near miss program and its implementation.
Tip #2 Encourage Consistent Near Miss Reporting
Whenever a near miss occurs or is reported, it is critical to not place the blame solely on the employee, as the root cause of a near miss is more likely to be a flaw in the organization’s systems or processes. Another way to encourage near miss reporting is to emphasize how it benefits employees by giving real-life examples of how it prevented an injury or saved a life.
Tip #3 Provide Near Miss Reporting Forms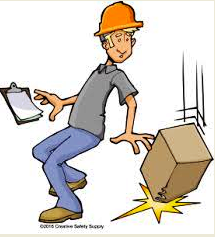
Save employees time spent on making near miss reports from scratch by providing near miss reporting forms that are easy to understand and fill out. A near miss reporting form should contain the following:
- Date, time, and location of the near miss
- Other details including the hazards involved
- Person affected by the near miss and witnesses
Conclusion
While it is not necessary to report near misses to OSHA, it is a great way to improve workplace safety and a vital step in any continuous safety improvement strategy. By normalizing near miss reporting as a standard part of everyday working life, you ensure that safety is a priority for all staff.
A workplace culture focused on improving safety and looking out for one another leads to increased morale and productivity. You’re saving money in the long run, as well as taking care of the people working hard for the success of the company.
Click the below links to know more details about near miss PPT, TBT, and Signages
Near Miss -PowerPoint presentation-Part-1
Near Miss -PowerPoint presentation-Part-2