Material safety data sheet:
Introduction :
A Material Safety Data Sheet is a document that contains information on the potential hazards (health, fire, reactivity and environmental) and how to work safely with the chemical product. It is an essential starting point for the development of a complete health and safety program. It also contains information on the use, storage, handling and emergency procedures all related to the hazards of the material. The MSDS contains much more information about the material than the label. MSDSs are prepared by the supplier or manufacturer of the material. It is intended to tell what the hazards of the product are, how to use the product safely, what to expect if the recommendations are not followed, what to do if accidents occur, how to recognize symptoms of overexposure, and what to do if such incidents occur.
Do I need an MSDS: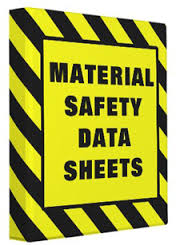
In Canada, every material that is controlled by WHMIS (Workplace Hazardous Materials Information System) must have an accompanying MSDS that is specific to each individual product or material (both the product name and supplier on the MSDS must match the material in use).
What information is on the MSDS:
There are nine (9) categories of information that must be present on an MSDS in Canada. These categories are specified in the Controlled Products Regulations and include:
- Product Information: product identifier (name), manufacturer and suppliers names, addresses, and emergency phone numbers.
- Hazardous Ingredients.
- Physical Data.
- Fire or Explosion Hazard Data.
- Reactivity Data: information on the chemical instability of a product and the substances it may react with.
- Toxicological Properties: health effects.
- Preventive Measures.
- First Aid Measures.
- Preparation Information: who is responsible for preparation and date of preparation of MSDS.
The Controlled Products Regulations prescribes what information must be present in more detail.
Why is my MSDS so hard to understand?
Traditionally the intended readers of MSDSs were occupational hygienists and safety professionals. Now the audience also includes employers, workers, supervisors, nurses, doctors, emergency responders and workers. To ensure that MSDS users can quickly find the information that they need, the information should be in an easy-to-read format and written in a clear, precise and understandable manner.
For most people who work with controlled products, there are some sections that are more important than others. You should always read the name of the chemical, know the hazards, understand safe handling and storage instructions, as well as understand what to do in an emergency.
Is all the information I need on the MSDS?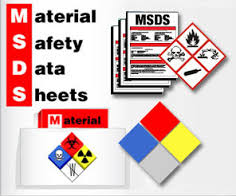
Not necessarily. A lot of health hazard information, for example, is written in general terms. Your health and safety specialist, occupational health nurse or family doctor should be able to help you find more information if needed.
When would I use an MSDS?
Always be familiar with the hazards of a product BEFORE you start using it. You should look at a MSDS, match the name of the chemical on your container to the one on the MSDS, know the hazards, understand safe handling and storage instructions, as well as understand what to do in an emergency.
Why do some MSDSs look different?
MSDSs look different because only certain content of the MSDS is specified by law. The format is left up to the manufacturer or supplier who writes the MSDS. Some manufacturers/suppliers put more details in than what is required. However, the information for the nine basic categories must always be in a Canadian MSDS for a controlled product.
Can an MSDS be too old?
Yes. Under WHMIS law, an MSDS for a controlled product must not be more than three years old. If you are still using a product that you bought more than three years ago, you may not have a current MSDS. Contact the manufacturer or supplier again and ask for a newer version of the MSDS.
The three-year time limit does not apply to MSDSs for non-controlled products (i.e. products that do not meet WHMIS criteria).
How often should an MSDS be updated?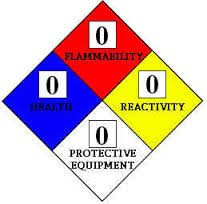
If new, significant information becomes available before the three years has elapsed, the supplier is required to update the product label and MSDS.
If there is no new information on the ingredients by the end of the three-year period, the supplier should review the MSDS and the label for accuracy, revise it where necessary, and revise the preparation date on the MSDS.
As an employer, do I have responsibilities for MSDSs?
Yes. Employers must make sure that all controlled products have an up-to-date (less than three years old) MSDS when it enters the workplace. The MSDSs must be readily available to the workers who are exposed to the controlled product and to the health and safety committee or representative. If a controlled product is made in the workplace, the employer has a duty to prepare an MSDS for any of these products.
Employers may computerize the MSDS information as long as all employees have access to and are trained on how to use the computer, the computers are kept in working order, and that the employer makes a hard copy of the MSDS available to the employee or safety and health committee/representative upon request.
Material safety data sheet(MSDS):
This section will aid writers in identifying the specific types of information required in MSDSs used in Canada, the US and the European Union. This document is not intended to be a comprehensive guide on how to write MSDSs but it will provide information that will be useful to MSDS writers.
Many countries have legislation that requires chemical producers or suppliers to prepare MSDSs. In Canada this legislation is generally called WHMIS (Workplace Hazardous Materials Information System). The Controlled Products Regulations (CPR) define technical criteria for determining if a material is hazardous (a controlled product) and what information must be contained on labels and MSDSs. These regulations are commonly referred to as the "WHMIS regulations".
The WHMIS regulations specify requirements for a 9-section MSDS. However, since the WHMIS regulations were passed, several agencies have made recommendations or approved standards for the format and content of 16-section MSDSs. These agencies include the International Labour Organization (ILO), the European Union (EU, formerly the European Communities, EC), the American National Standards Institute (ANSI), and the International Organization for Standardization (ISO). The 16-headings for MSDSs, described in more detail below, have been approved for use in WHMIS-compliant MSDSs if two conditions are met. First, all the information required in the Controlled Products Regulations must be in the MSDS. Second, a statement like "This product has been classified according to the hazard criteria of the CPR and the MSDS contains all the information required by the CPR." appears under heading "Section 15 - Regulatory Information".
How do I make hazard identification and classifications?
The first step in preparing an MSDS is to collect information about the material and its components including physical, chemical and environmental characteristics, and toxicity information. The collected information is then evaluated and assessed to determine the potential physical (fire and reactivity), health and environmental hazards associated with the material. Then, using professional judgement, the product is classified according to the hazard criteria specified in legislation of the country where the product will be used. The corresponding Canadian legislation is the Controlled Products Regulations (CPR), made under the Hazardous Products Act. This legislation defines the criteria for categorizing controlled products into various classes. Several classes have subclasses to provide more specific information about particular kinds of hazards. The CPR should be consulted to find out what the criteria are that are used to classify chemical products as flammable versus combustible or toxic versus very toxic, and so on.
The Controlled Products Regulations (WHMIS) regulations also prescribe what elements of information must be on labels and MSDSs for WHMIS-controlled products. The supplier must use professional, scientific judgement when evaluating the test results of the product or, where appropriate, a product with similar properties. The supplier also has the duty to report any hazard information of which he or she is "aware or ought reasonably to be aware" [see subsections 12(11) and 33(2) of the CPR]. The toxicology information must be presented in such a way "so as not to mislead a person as to the nature or extent of the hazard posed by the controlled product" [subsection 13.1].
Information is to be disclosed on a MSDS:
In Canada the Controlled Products Regulations (see Schedule I below) specify what information must be disclosed in an MSDS. In the US, the OSHA Hazard Communication Rule (29 CFR1900.1200) prescribes what information is to be provided by MSDS. Those who prepare MSDSs for chemical products used in workplaces in other countries should consult the legislation in those jurisdictions to find out their requirements for product classification, labelling and information to be disclosed in MSDSs.
International standards and guidelines for preparing MSDSs:
When WHMIS came into effect in 1988, there were no national or international standards for MSDS formats. Since then several guidelines and standards have been prepared. One such standard is the American National Standard for Hazardous Industrial Chemicals - Material Safety Data Sheets - Preparation (ANSI Z400.1-2004). This standard specifies:
- the general layout of MSDSs
- 16 headings with standardized wording.
- the numbering and order of these headings.
- the information items required to complete an MSDS
The objective of this standard is to "create consistency in providing information on safety, health and environmental matters for chemical products". The 16-section MSDS headings in the standard are the same as those proposed for adoption by the Globally Harmonized System of Classification and Labelling of Chemicals (GHS). The GHS addresses the classification of chemicals by types of hazard (health, fire, reactivity, environmental) and proposes harmonized hazard communication elements (labels and safety data sheets). It is intended that the GHS will be adopted worldwide.
Please see the OSH Answers Globally Harmonized System (GHS) for general information on GHS.
Canadian regulatory authorities have said that they will accept the 16-heading format if all the information required by the CPR is included. They also require a statement such as "This product has been classified according to the hazard criteria of the CPR and the MSDS contains all of the information required by the CPR" be entered in the "Regulatory Information" section.
Table 2 itemizes the WHMIS MSDS headings suggested in Schedule I of the CPR along with the headings specified in standards for the 16-heading format.
MSDS require in comparison to other standards (ANSI, GHS):
ANSI standard for preparing MSDSs:
The ANSI "Standard for Hazardous Industrial Chemicals - Material Safety Data Sheets - Preparation" (ANSI Z400.1-2004) is a consensus standard. It was prepared by a committee with user input from numerous labour representatives, government officials, professional associations, industry associations and academic groups.
Even though the ANSI standard was prepared in the US, the standard is useful to MSDS preparers around the world. The ANSI standard describes the format for MSDSs and discusses the various steps involved in preparing MSDSs such as how to:
- collect information.
- determine hazards of materials.
- complete each section of an MSDS.
- organize and present the information in the MSDSs
The standard has information about the appearance and readability of MSDSs. It explains where technical and non-technical language should be used to optimize MSDS usefulness to different groups of readers. For example, medical information can be provided under the subheading "Notes to the Physician" in the section "First Aid Measures". Non-technical language should be used in sections intended for use by the employee (e.g., under the subheading "First Aid Procedures"). It also provides advice about font types and sizes, page layouts and so on that make MSDSs easier to read.
The standard also provides a list of commonly used phrases and the extensive glossary to help suppliers write MSDSs clearly without an extensive use of technical terms or jargon. For example, the phrase " . . . may cause partial to complete unconsciousness" will be clearer to many readers than " . . . causes narcosis". To prevent skin contact, "wear chemical resistant clothing such as gloves, apron, boots or whole body suits made from Neoprene, as appropriate" is more precise and helpful than "wear chemical resistant clothing". It also provides some sample MSDSs and a brief checklist for evaluating the completed MSDSs.
What are the main differences between the 1998 ANSI Standard compared to the 2004 standard?
The 2004 revision states that the new standard includes the following significant changes:
Improving hazard communication and aligning the Standard with the recommendations for safety data sheets in the Globally Harmonized System for Hazard Classification, Communication and Labelling (GHS) adopted by the United Nations in 2002;
- Improving readability and consistency and minimizing redundancy;
- Reordering the MSDS sections so Hazards Identification appears before Composition Information;
- Including a requirement that flammable properties appear in the physical and chemical properties section with an option to repeat them in the fire fighting measures section;
- Increasing consistency between the sections for Toxicological Information and Ecological Information, and including more complete and accurate lists of data types;
- Adding transportation elements that may be needed for transporting a chemical by various modes, to meet international regulations and for improved emergency response.
Safety Data Sheets (SDS):
What is a Safety Data Sheet?
A Safety Data Sheet (SDS), previously called a Material Safety Data Sheet (MSDS), is a document that provides information on the properties of hazardous chemicals and how they affect health and safety in the workplace. For example an SDS includes information on:
- the identity of the chemical,
- health and physicochemical hazards,
- safe handling and storage procedures,
- emergency procedures, and
- disposal considerations.
The SDS should always be referred to when assessing risks in the workplace.
What information needs to be provided on a SDS?
The safety data sheet shall be dated and shall contain the following headings:
1. Identification of the substance/mixture and of the company/undertaking;
2. Hazards identification;
3. Composition/information on ingredients;
4. First-aid measures;
5. Fire-fighting measures;
6. Accidental release measures;
7. Handling and storage;
8. Exposure controls/personal protection;
9. Physical and chemical properties;
10. Stability and reactivity;
11. Toxicological information;
12. Ecological information;
13. Disposal considerations;
14. Transport information;
15. Regulatory information;
16. Other information.
When should a SDS be updated?
There is no statutory review period for revising a SDS; however, it needs to be updated:
- As soon as new hazard information or information that may affect the risk management measures becomes available; or
- When a substance or mixture is classified according to the CLP Regulation (see also section on ‘how will the CLP Regulation affect SDS?’)
- Once an authorisation under REACH is granted or refused; or
- Once a restriction under REACH has been imposed.
- When a SDS is updated, the new dated version of the SDS, identified as ‘Revision: date’, shall be supplied to all customers (of the substance/mixture in question) from the preceding 12 months.
What is REACH:
REACH (Registration, Evaluation, Authorisation and restriction of Chemicals) is the system for controlling chemicals in Europe. It became law in the UK on the 1st June 2007. REACH adopted some of the older aspects of the chemicals system in Europe, including Safety Data Sheets (SDS).
Previously, under the Chemicals (Hazard Information and Packaging for Supply) Regulations 2002 (CHIP) suppliers of substances or mixtures meeting the criteria for classification as dangerous have, been required to compile and supply a SDS at the first delivery of a substance or mixture.
REACH took over this system and it has now been changed to take into account the new Classification, Labelling and Packaging (CLP) Regulation.
Do you need to provide a SDS?
You need to provide a SDS if:
1. You supply a:
(a) substance or a mixture (see definitions section below) that is classified as dangerous under Dangerous Substances Directive 67/548/EEC or Dangerous Preparations Directive,1999/45/EC or classified as hazardous under the CLP Regulation (EC) No 1272/2008; or
(b) a substance that is persistent, bioaccumulative and toxic (PBT), or very persistent and very bioaccumulative (vPvB) as defined in Annex XIII of REACH ; or
(c) a substance that included in the European Chemicals Agency’s 'Candidate List' of substances of very high concern (SVHC see ‘definitions section below) for reasons other than (a) and (b) given here.
2. You are a supplier and your customer requests a SDS for a mixture that is not classified as dangerous under Directive 1999/45/EC, but contains either:
(a) a substance posing human health or environmental hazards in an individual concentration of ≥ 1 % by weight for mixtures that are solid or liquids (i.e., non-gaseous mixtures) or ≥ 0.2 % by volume for gaseous mixtures; or
(b) a substance that is PBT, or vPvB in an individual concentration of ≥ 0.1 % by weight for mixtures that are solid or liquids (i.e., non-gaseous mixtures); or
(c) a substance on the 'Candidate List' of substances of very high concern (for reasons other than those listed above), in an individual concentration of ≥ 0.1 % by weight for non-gaseous mixtures; or
(d) a substance for which there are Europe-wide workplace exposure limits. If you are a supplier to EU countries other than the UK, then you may need to supply a SDS for substances or mixtures that are not classified as dangerous where they have relevant national workplace exposure limit values.
SDS Signage:
Click the below link to download safety moment and animation video
Safety Animation video- Hazard communication