Incident analysis methods:
Introduction:
The models used in accident investigation can typically be grouped into three types: sequential, epidemiological, and systemic models. Although the sequential and epidemiological models have contributed to the understanding of accidents; they are not suitable for clarifying the complexities and dynamics of modern sociotechnical systems.
In these systems, the interactions and events are connected in complicated ways, and standard safety engineering techniques alone are not sufficient to comprehend the accident causation. When analyzing major accidents in process industries, a more systematic and professional model is needed than when supervisors and workers are investigating a normal minor accident in a simple setting.
What are incidents?
An incident is an unplanned event or chain of events that results in losses such as fatalities or injuries, damage to assets, equipment, the environment, business performance or company reputation. A near miss is an event that could have potentially resulted in the abovementioned losses, but the chain of events stopped in time to prevent this. These incidents can be classified in all kinds of severities and types, and thus into categories. Investigation and cause analysis should take these different categories into consideration.
Purpose of investigation:
The purpose of this Incident Investigation Guide is to provide employers a systems approach to help them identify and control the underlying or root causes of all incidents in order to prevent their
recurrence.
The Bureau of Labor Statistics reports that more than a dozen workers died every day in American workplaces in 2013, and nearly 4 million Americans suffered a serious workplace injury. And tens of
thousands are sickened or die from diseases resulting from their chronic exposures to toxic substances or stressful workplace conditions. These events cause much suffering and great financial loss to workers and their families, and also result in significant costs to employers and to society as a whole. Many more “near misses” or “close calls” also happen; these are incidents that could have caused serious injury or illness but did not, often by sheer luck. Practically all of these harmful incidents and close calls are preventable.
All incidents – regardless of size or impact – need to be investigated. The process helps employers look beyond what happened to discover why it happened. This allows employers to identify and correct shortcomings in their safety and health management programs.
Incident investigations help employers:
- Prevent injuries and illnesses
- Save lives
- Save money
- Demonstrate commitment to health and safety
- Promote positive workplace morale
- Improve management
The Need for a Methodology:
One fascinating yet troubling phenomenon that often goes unnoticed during incident investigations is that individual beliefs play a major determining role in the outcome, because those outcomes depend partly on where the investigators believe the root cause lies. This includes opinions and
assumptions the investigator has at the beginning along with prejudices formed along the way. It goes even deeper than individual beliefs about how accidents happen, however. Even experienced and well-trained safety professionals sometimes are biased in that they support causation models
which may not tell the full story of how incidents came about.
Frequently, an investigation team’s bias can result in narrowly-focused cause analysis. This shortcoming can result in avenues of investigation being left unexplored, which can happen when investigation teams are influenced by their preconceived notions, or jump to conclusions.
Rarely is a single factor to blame in isolation for an event that results in serious harm. An important lesson is that “disasters are very rarely the product of a single monumental blunder.” Thorough root cause analysis often uncovers surprising results, which underscores the reason letting preconceived notions guide the process may result in never finding the real cause. Worse yet, failing to mitigate the actual root cause puts lives and assets at continued, preventable risk. Indeed, there’s prevailing and persistent misinformation in the industry, causing many EHS professionals to mismanage their incident investigation initiative.
Getting past assumptions: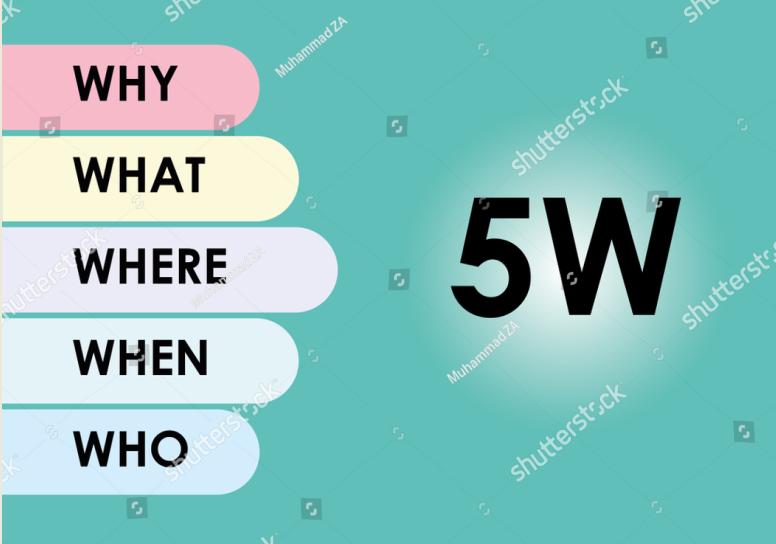
Many practitioners are misguided by a persistent myth in the industry. The myth that’s persisted for at least half a century is that workers committing unsafe practices are the cause of most incidents in the work place. It has been stated2 that the causes of industrial accidents could be broken down in this way:
- 88% caused by “unsafe acts of persons”
- 10% caused by “unsafe mechanical or physical conditions”
- 2% unpreventable
Believe it or not, many of the incident investigations performed even today are permeated by
this 88-10-2 formula. It’s still taught in educational programs at universities and is therefore extremely entrenched in the incident management community. Due to lack of knowledge and bad beliefs, many EHS Professionals are not using effective causation models.
The persistence of this type of misconception is one of the major reasons why companies find a
rigorous incident investigation methodology to be an incredibly helpful and powerful addition to
their EHS program. A well-defined investigation methodology assists investigators in finding the ac can be implemented.
METHODOLOGIES & MODELS:
n investigation methodology is how you think about, understand and resolve root causes of an incident. While software can support the process, the right methodology must first be selected and implemented.
The incidents we investigate— accidents and near misses—almost never result from one cause. Most of them involve multiple, interrelated causal factors. This complexity should also be reflected in the investigation methodology used. Selecting the right one for your situation can be
challenging.
Before we dive into some example methodologies, let’s look at some analytical models. This will help us think about the methodologies in the following sections.
Systemic models
focus on the systems and processes of the organizational culture and leadership to understand accident causes as mismatches or failures between those components.
Logical tree models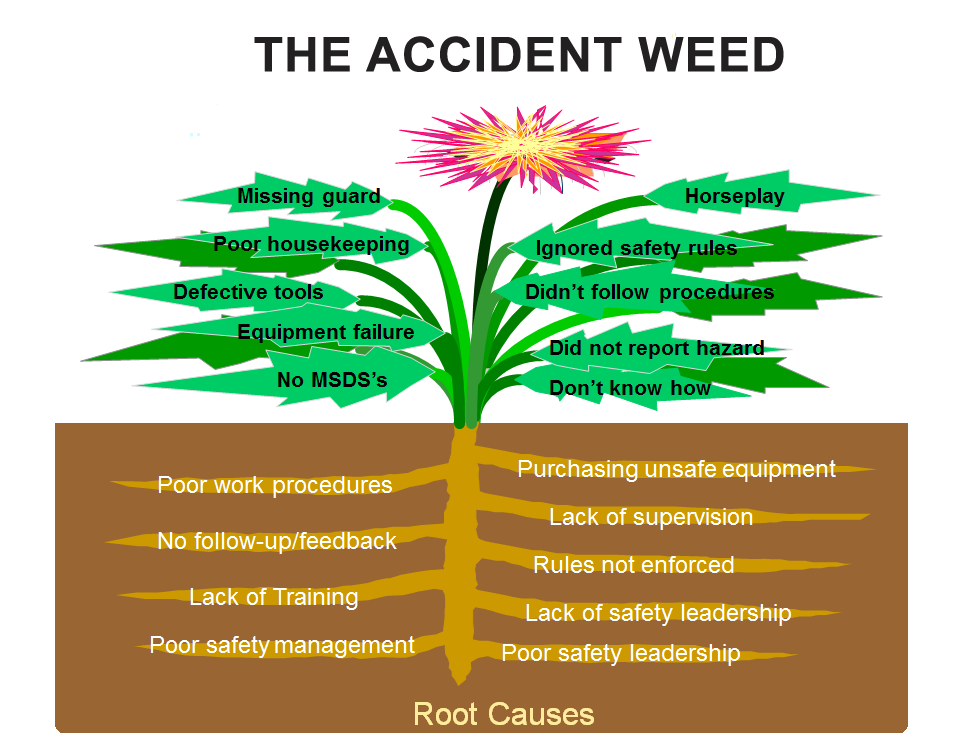
attempt to analyze the causes of accidents as a set of events and conditions, paying particular attention to the logical relationships between them.
Sequence-of-Events
(Domino, or Causal-sequence) models evaluate accidents as a continuous set of failures that set off a chain reaction.
Epidemiological models
from the medical term for the spread of disease, investigate accidents as emanating from hidden
failures across all organizational components, including management, procedure and design.
Energy model
rooted in epidemiology, focuses on the transfer of energy causing injury to a person, and therefore seeks to find ways to prevent such a transfer.
Process models
focus on ways in which a production system can deteriorate over time, making a clear distinction between a sequence of events and any underlying causal or contributing factors.
Human information-processing models
analyze the situation from the perspective of a human operator and his interaction with his environment.
EHS management models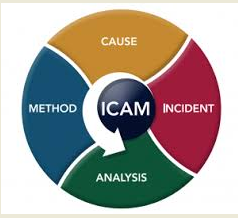
explore the possible contributing and causal factors related to the failings of the organization and its management.
We’ll introduce at least one methodology as an example of each of the analytical models we just listed. These models help us understand how a particular methodology could be used to identify the direct causes and contributing factors of incidents. They can be used to evaluate and ultimately reduce the number of direct causes to which further analysis will be applied.
The best methodologies help investigators by utilizing multiple models of analysis to ensure
thorough research into root causes and contributory causes. Some of the methodologies discussed could be described as diagramming techniques. These can provide a useful framework for developing evidence by summarizing the events in a diagram, which provides a framework for
documenting evidence, identifying causal factors, and identifying gaps in knowledge.
Diagrams help prevent inaccurate conclusions by exposing gaps in the logical sequence of events. Where gaps are identified, further analysis can uncover necessary detail.
The best methodology for you might be a combination of several tools or methodologies. Some of those covered in the following sections are really a combination of tools and techniques that are assembled together to form a new methodology. Nothing prevents you from doing the same thing to make an ideal methodology for your organization
SYSTEMATIC CAUSE ANALYSIS TECHNIQUE (SCAT)
The International Loss Control Institute (ILCI) developed SCAT about 20 years ago for the purpose
of occupational health and safety incident investigations.
SCAT is a systemic Model focused on the systems and processes of the organizational culture and leadership, and is based on root cause analysis methods. This methodology provides a chart with a
series of cross referenced categories. The investigator must identify the relevant factors by working
systematically through the chart and identifying the contributing factors within each category.
Issues which lead to an incident are described as points at which the organization loses control over deficiencies, which in turn led to the undesired outcome.
In other words, SCAT asks investigators to go back before the cause of the problem to where the roots of that cause were formed. One cause might be inadequate leadership, for example. The following figure depicts the pathway of investigation in the SCAT method. As illustrated below, five
main points - lack of control, basic causes, immediate causes, incident, and loss - are used in this type of systemic technique.
SCAT: Systematic Cause Analysis Technique
MANAGEMENT OVERSIGHT & RISK TREE (MORT)
The Management Oversight and Risk Tree (MORT) is an analytical procedure for determining causes and contributing factors. It arose from a project undertaken in the 1970s to provide the U.S. Nuclear industry with a risk management program competent to achieve high standards of health and safety.
MORT, a logical tree model, is based on Fault Tree Analysis (FTA), a top down, deductive failure analysis procedure used to analyze causes and related factors of an undesired state using Boolean logic to combine a series of lower-level events and precursors.
Fault tree analysis maps the relationship between faults, subsystems, components, and controls by creating a logic diagram of the overall system.
Every sufficiently complex system is subject to failure as a result of one or more individual components failing.
MORT uses a comprehensive analytical procedure that provides a disciplined method for determining the causes and contributing factors of major accidents. The method can also be used to proactively evaluate the quality of an existing system.
Accidents are defined as unplanned events that produce losses when a harmful agent comes into contact with a person or asset. This contact can occur because of a failure of prevention or as an unfortunate, but acceptable, outcome of a risk that has been properly assessed and assumed. Most of the effort is directed at identifying problems in the control of a work process and deficiencies in the barriers involved, as in:
1. a vulnerable target exposed to...
2. an agent of harm in the...
3. absence of adequate barriers.
The MORT methodology is less-used today in whole, but the charting technique is fairly common.
SEQUENTIAL TIMED EVENTS PLOTTING (STEP):
A technique that can be used to depict a basic timeline of an incident is the Sequential Timed
Event Plot5 also known as a STEP diagram. Events, activities, and state changes can be organized into a single diagram in a sequence-of events analytical model.
The timeline can focus primarily on ‘what’ happened (the events) and less on why things happened (the causes). This is because there may be multiple (interacting) causes for any event on the timeline and causes may not be close together in time or place.
While other methodologies may be more helpful to identify the root causes of accident consequences, STEP can be extremely beneficial for understanding the interaction between multiple factors and outcomes. The timeline-based approach clearly and concisely gives a picture of the ‘what’ and ‘when’ to allow investigation teams to work backwards to the ‘why’ and the ‘how’.
STEP is a multilinear systems approach that view accidents as multiple avenues of causal factors
that are interrelated and interact with other factors throughout the system to ultimately lead to an
accident.
The STEP procedure relies on a worksheet that provides structure, visibility, and organization to data gathering and analysis. It graphically represents the beginning and end of an accident sequence, detailing actors and actions over time. The procedure accommodates events that occurred at the same time. These events allow investigators to visually recreate the mental map of
a sequence of events and determine gaps.
BARRIER ANALYSIS METHOD:
barrier analysis provides a structured method of evaluating the events related to a system failure or incident. It is largely an energy model, used to find and evaluate ways of avoiding unwanted energy transfer. The term barrier encompasses a wide range of concepts such as personal protective
equipment, machine guards, and alarms. Additionally, barriers could include preventative measures such as standard operating procedures, work instructions, training, supervision, emergency plans, safety reviews, risk assessments, and Lockout/Tagout procedures.
Barrier Analysis might begin with analysis of the physical, human action, natural, and administrative controls that should be in place. The sequence of events are evaluated to determine which barriers failed or succeeded. Additionally, the analyst should determine if certain barriers could have prevented the incident if they had been put into place.
Barrier analysis is often used in conjunction with MORT. More recently, it has been used with bowtie diagrams and even adapted for use with SCAT.
CHANGE ANALYSIS METHOD
Change Analysis uses a process model to focus on ways in which a production system can deteriorate over time. In this method of analyzing system failures, the investigator searches for a change or changes in the system that led to failure. The method assumes change is the culprit because the system performed adequately for a period of time and then suddenly failed.
Two important concepts in this method are the directional and exponential characteristics of change. The directional characteristic of change proposes that if a change is made the system will continue in that direction unless another change is made towards a new direction or back toward the original state. The exponential characteristic of change says that when multiple changes are made their combined effect is said to affect the system exponentially rather than additively. This change analysis technique begins with a comparison between the state of the system just before
the incident and the state of the system during the incident. The analyst establishes the differences and evaluates the contributions of each difference. Worksheets are often used to guide the investigator using change analysis to consider factors of the changes:
- What
- Where
- When
- Who
- Nature of the Task
- Working Conditions
- Presence of a Trigger Event
- Relevant Managerial Controls
The analyst examines the incident situation, considering comparable non-failure states. The comparison of the failure situation with nonfailure states produces a list of differences between the two situations. A trained investigator can use the contrast between failure and non-failure states to identify key differences and analyze the roles these differences played in the incident’s causal factors.
INCIDENT CAUSE ANALYSIS METHOD (ICAM)
Human Performance Investigation Process (HPIP) was developed for the US Nuclear Regulatory
Commission (NRC) for use by NRC investigators. This composite, ESH management focused methodology is comprised of a suite of six tools:
Events and Causal Factors Charting – A tool used to plan the investigation, similar in some regards to the STEP diagrams already covered. The chart contains the sequence of events and
the potential causal factors that led to the accident.
SORTM – A guide to HPIP Modules used to assist investigation planning, fact collection, and identification of human performance difficulties for root cause analysis.
Barrier Analysis – A technique to identify human performance difficulties for root cause analysis,
basically covered in a preceding section.
HPIP Modules – Identifies human performance difficulties and programmatic system weaknesses.
Each module, such as Training or Procedures, is broken down into a set of Near Root Causes, such as No Training. Finally, each of those is broken down into a set of Root Causes, such as No Learning Objective. Getting to the bottom of the tree of relationships, the investigator is guided by a series of preformulated questions.
Change Analysis – Allows understanding of the event and ensures complete investigation and
accuracy of perceptions. This also as covered in a preceding section.
Critical Human Actions Profile (CHAP) – Similar to change analysis, CHAP provides an understanding of the event and ensures complete investigation and accuracy of perceptions. It is an operationally oriented technique based on human factors task analysis.
INCIDENT CAUSE ANALYSIS METHOD (ICAM)
Incident Cause Analysis Method (ICAM) is based on the work of James Reason, who was a professor of psychology at the University of Manchester in the United Kingdom. Reason’s primary area of focus was on understanding “Human Error” as it related to accidents, and the ICAM model is based on his Swiss Cheese, Defenses in Depth model of incident causation.
According to Reason, very few unsafe acts result in actual damage or injury. Various layers of defense can only be breached by the adverse conjunction of several different causal factors.
A foundational concept of ICAM is inevitability of human error. Human factors research has shown
that human error is a normal characteristic of human behavior, and although it can be reduced, it
cannot be completely eliminated. ICAM is designed to ensure that the investigation is not restricted to the errors and violations of operational personnel.
It helps identify other factors that contributed to an incident in order to identify root causes, and make recommendations on corrective actions to prevent recurrence.
MANY OTHER AVAILABLE METHODS
There are several popular methodologies available which require license fees, and are strictly controlled under copyright. Therefore, use of such a methodology might limit your options when obtaining training for your staff, and your ability to modify or evolve the methodology for your
particular industry or organization. However, if you are looking for an out of the box solution, these
methodologies are fairly common and well-respected by many organizations.
- Tap RooT
- REASON
- Kelvin TOP-SET
Still other tools are prevalent and not so strictly controlled. Consider these if you want some readily available training, yet also the flexibility to modify the methodology for your own unique circumstances.
Some examples include
- The “5 Why” Method
- Man, Technology and Organization (MTO) Analysis
- Functional Resonance Accident Model (FRAM)
- Human Factors Analysis and Classification System (HFACS)
- Systems Theoretic Accident Modeling and Processes (STAMP)
- AcciMap
- Safety Occurrence Analysis Methodology (SOAM)
- Accident Evolution and Barrier Function Method (AEB)
- Safety Function Analysis (SFA)
- Tripod Delta
Decades of research have provided a numerous models and methodologies to choose from. Incident investigators have such a wide array of tools available, it can be challenging to find the right ones. We hope this helps encourage them
Although we’ve only provided a single example methodology of each model type, there are many
more to research and evaluate. When designing or selecting a methodology, it is wise to research
and evaluate several.
Selecting a suitable accident investigation technique: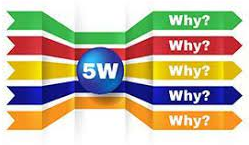
It is essential that workplaces have a plan about how to investigate accidents. Irrespective of the technique, it is important that those persons who are involved in accident investigation know how to conduct the investigation and are aware of the guidelines for investigating accidents in their workplace. The persons who participate in these investigations should be named (usually safety managers and supervisors) and in addition, a worker from the accident scene may beneficially be included in the investigation.
When selecting a suitable technique for accident investigation, there should be at least one person who has a good knowledge about the different accident investigation techniques suitable for use in their work environment, and who is able to choose the proper method for each case. Some minor accidents may not need to be investigated in the same kind of depth as those that have led to serious injuries.
Conclusions:
Accidents and also near misses almost never result from one single cause, most accidents involve multiple, interrelated causal factors. All actors or decision-makers influencing the normal work process might also influence accident scenarios, either directly or indirectly. This complexity should also be reflected in the accident investigation process. The aim of accident investigations should be to identify the event sequences and all (causal) factors influencing the accident scenario in order to be able to propose risk reducing measures which may prevent future accidents.
Often, accident investigations involve using a set of accident investigation methods. Each method might have different purposes and may make their own contribution to the total investigation process. It is important to remember that every piece of a puzzle is as significant as the others.
Graphical illustrations of the event sequence are useful during the investigation process because they provide an effective visual aid that summarizes key information and provides a structured method for collecting, organizing and integrating collected evidence to facilitate communication between the investigators. Graphical illustrations also help to identify information gaps.
During the investigation process, different methods should be used in order to analyze emerging problem areas. There should be at least one member of the multi-disciplinary investigation team who has good knowledge about the different accident investigation methods, and is able to choose the optimal methods for analyzing the different problems.
Click the below links to download Toolbox talk, PPT and guidelines for Accident investigation technique
Toolbox talk - Accident Investigation Responsibilities
PowerPoint presentation - Accident Investigation
PowerPoint presentation - Accident investigation Techniques
Accident Investigation technique guidelines