Hand protection:
Introduction:
Hand protection is saving one’s hands from any sort of injury at work. Hands are vital tools of human being and therefore most vulnerable to injuries as well. Very often, hands are exposed to hazardous conditions such as sharp edges, pinch points, rotary machinery, hot objects, electricity, splinters and chemicals etc. If hands are not protected and get injured, they will last for lifetime.
Hand Protection Gloves and the Law :
Specialist gloves can offer protection against many harmful substances and hazards, we well as ensuring that employers are compliant with legal requirements.
Across many industries and operations, workers are required to use their hands and this involves a level of potential risk which should always be considered by employers prior to any task being undertaken.
There are many factors an employer should consider when purchasing PPE gloves, with the main ones being:
- Which substances will be handled
- What hazards are likely to be encountered
- The type and duration of contact the gloves will need to withstand
- Who will be wearing the gloves - including their size and any personal requirements
- The job at hand, and any task-specific needs
Once you are clear on your specific requirements, take a look at our range of protective gloves to find exactly what suits your needs.
Regulations and Standards for Hand Protection:
When it comes to PPE hand protection, the legislation and standards you need to be aware of are as follows:
- Control of Substances Hazardous to Health Regulations (2002) - These regulations state that employers have a responsibility to protect workers from exposure to substances which could be hazardous to their health.
- Personal Protection Equipment Regulations (2002) - Under these regulations, PPE equipment must be fit for purpose and properly stored and maintained. Employees must also be properly instructed on how to use it.
- EN 420 - This is a European standard which lays out the general requirements which need to be met for PPE gloves to be fit for purpose. At Protec, all of our work gloves meet the EN 420 standards.
Common types of hand injuries include the following:
Traumatic injury occurs when hands and fingers get caught, pinched or crushed in chains, wheels, rollers, or gears of various machinery and get cuts to the skin, tendons, blood vessels and nerves, skin punctures, pricks, abrasion, irritation, bones fractures and sprains.
Contact or permeation injury occurs when our hands get contact with corrosive liquids, solvents, acids, detergents, flammable liquids and other substances and permeated through the skin. This can cause chemical burns or injure tissues, skin irritations, allergic dermatitis, major organ damage, carcinogenic effects etc.
Repetitive motion injury occurs when jobs require repeated, rapid hand movements for long period of time. Most of these injuries are musculoskeletal disorders.
Thermal injury occurs due to high temperatures of the equipment or fire while handling hot parts, thermoplastics molds, welding-cutting, foundry works, thermoforming, removing food from ovens etc. Thermal injury occurs in the form of burns, dermatitis, frostbite and blisters etc.
To protect our hands against these injuries we should do the following:
- Perform out risk assessment.
- Follow user manual and product labels.
- Use appropriate gloves (type, size and shape) and PPEs or barrier cream.
- Avoid using finger rings and ornaments such as bracelets or watches.
- Change grips, hand positions or motions. Give hands a rest.
- Use machine guards and safety devices etc at all the times.
- Lockout and switch off equipment and machines those are not in use.
- Wash hands when in contact with corrosive chemicals or as appropriate.
General Requirements: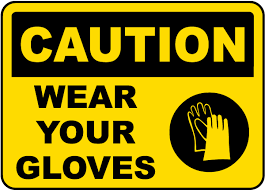
Hand and arm protection must be selected and used when personnel may be exposed to certain hazards, such as:
- Work with harmful substances, dry or liquid, that can be absorbed through the skin, or that can cause skin irritation, chemical burns, or similar conditions. Examples would include strong acids/bases, toxic or corrosive materials, organic solvents, and radioactive materials.
- Work with tools, equipment, or materials that can cause cuts, lacerations, punctures, fractures, amputations, or abrasions.
- Work where the employee is exposed to materials or agents that can cause thermal burns or that expose the employee to harmful temperatures.
- Work that may expose employees to blood or other potentially infectious agents.
- Work on live electrical systems or components. Additional training is required for the use of electrical protective equipment.
The best place to start when selecting gloves for a task is to compare the exposure hazards to the protective qualities of the gloves available from your supplier. Many tasks will involve multiple hazards, and the glove selected should either protect against all of the hazards, or more than one type of glove may have to be worn. A common example of this is when leather gloves (cut/puncture/abrasion resistant) are worn over voltage-rated rubber gloves. Certain chemical and/or radiation hazards may require double gloving (of the same type).
Potential Hazards:
Injuries and illnesses such as:
- Skin absorption of harmful substances
- Cuts or lacerations
- Abrasions
- Punctures
- Nerve or tendon damage caused by exposure to vibration
- Chemical burns
- Thermal burns
- Heat stress, frostbite, and hypothermia due to harmful temperature extremes
- Shocks and burns from electricity
Note: Improper selection of gloves may give workers a false sense of security since chemicals may penetrate the "protection" without it showing any signs of failure.
If you work in an industry which exposes workers to the above hazards, or other dangers, it’s vital to make sure they are properly protected with the right PPE gloves. It is important to note, however, that no glove material will protect against all substances, and gloves will often require replacement in line with manufacturer recommendations.
Types of PPE Gloves :
A wide range of hand and sleeve protection, providing the highest level of safety and security. In addition, all minimal risk work gloves conform to EN 420 (General Requirements for Gloves) and are CE marked, for your peace of mind.
A wide range of PPE gloves are available, including:
- Anti-vibration gloves
- Builders grip gloves
- Cut resistant gloves
- Disposable gloves
- General handling gloves
- Heat resistant gloves
- Leather gloves
- Nitrile coated gloves
- PU coated gloves
- Rigger gloves
- Protective sleeves
- Thermal grip gloves
Typical applications for our PPE gloves include medical, building, construction and trade specific requirements.
There are several categories of gloves.
Disposable gloves:
Perfect for one-time use situations. Thin for improved sensitivity and dexterity. Provides wearer protection against materials, or protects the material from the handler. Available in a variety of materials and for a variety of tasks.
Critical-environment gloves:
Used in applications that require extreme cleanliness, such as in the electronic, nuclear, and pharmaceutical industries.
Chemical-resistant gloves:
Protects against specified chemicals and liquids, also protects against abrasion, cuts, punctures, and snags. Generally, any "chemical-resistant" glove can be used for dry powders. (See additional information provided later in this section.)
General-purpose gloves:
Intended to help reduce hand injuries from snags, punctures, abrasions, and cuts.
Coated gloves :
Nitrile and natural rubber coated gloves are often used as substitutes for leather gloves. They offer superior hand protection in wet environments where dexterity is important.
Cut-resistant gloves: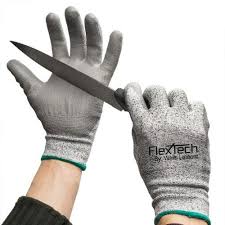
Available in a wide variety of materials, including metal-mesh, Kevlar, aluminized, etc. Protects against cuts and scrapes in the food industry, as well as general warehousing.
Puncture-resistant gloves: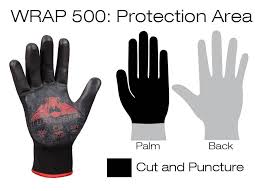
Available in a wide variety of materials. Puncture-resistant gloves protect against most sharp objects, including glass, metal, and needle sticks. No glove is completely puncture-proof, nor can gloves be expected to take the place of proper engineering or work practice controls.
Anti-vibration/impact gloves:
Protection from vibration or impact from tools and equipment. Helps prevent hand, finger, and arm fatigue.
Leather gloves: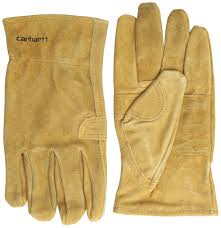
Qualities of leather include comfort, durability, dexterity, mild heat resistance, and abrasion resistance. Good all-purpose glove.
Temperature-resistance gloves: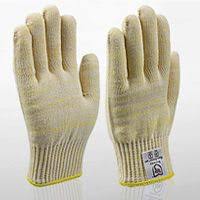
Provides protection from high temperatures as well as cold. Leather, Kevlar, cotton terrycloth, cryogenic gloves, rubber, Nomex, Zetex, and Flextra are some common materials used in this type of glove. Includes welding gloves.
Voltage-rated gloves:
Protection against shock hazards. To assure adequate electrical protection, choose the properly rated insulated gloves and protectors for your application. Additional training from EHS is required.
Different Potential hazards and its images
FROSTBITE
ABRASION
PENETRATION
FRACTURE
ELECTRICAL BURNS
BITES
LACERATION
PUNCTURE
Selection:
Workplace risks and hazards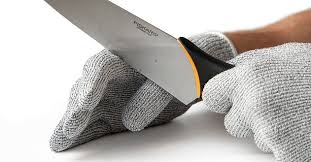
The following two sections provide a non-exhaustive list of the mechanical and other risks and
hazards relevant to the selection of protective gloves . It is possible that certain hazards encountered in a particular workplace will not be mentioned. Risk analysis carried out at the beginning of the glove-selection process should facilitate an evaluation of all of the risks at hand, whether they are linked to the execution of the task or to the particular work environment.
Mechanical hazards
The principal mechanical risks include cuts, punctures, medical needle punctures and abrasions.
Tearing per is not associated with a specific risk, but provides information on the mechanical
resistance of the glove [AFNOR, 2004]. All risks currently come under international, American and /or European standards.
Cut:
The risk of cuts by sharp objects, such as blades (knives), glass or metal, is present in many
work environments, including metal machining, food preparation and glass working. Fibres
providing good resistance to cuts are, for example, Kevlar, Spectra and Dyneema. Thin steel wires or glass fibres can be integrated into the knit glove to increase its resistance to cuts. Some gloves are made from metal loops or plaques. Recently, materials such as Super Fabric and Turtle Skin have been developed to provide better resistance to cuts and other hazards. It is important to remember that no glove is cut-proof.
Puncture: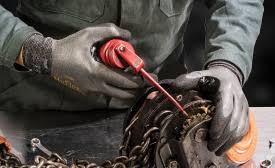
Workplaces contain various sources of risk for puncture: nails, wood or metal splinters, plant thorns, as well as numerous tools. Examples of work environments where these risks are present include metal machining, horticulture and mechanics. The resistance of gloves that must be worn to protect hands from the risk of puncture is linked primarily to the type and thickness of the materials making up the glove. Gloves coated with nitrile or polyurethane may provide a certain level of protection against puncture.
Tear:
Tear resistance provides us with information on the mechanical resistance of a glove, but does not indicate the protection provided against any specific risk [AFNOR, 2004]. Tearing is associated with the initiation and propagation of a crack in a material under very high stress. The tear often originates where there is a defect / a snag in the material, or where a large deformation is applied. Generally, in all work environments, situations arise in which a glove may tear. Gloves providing good tear resistance are often made up of highly tensile resistant fibres, coated with an elastomer such as nitrile or polyurethane.
Abrasion:
Abrasion is characterised by the gradual removal of surface matter owing to repetitive mechanical action such as rubbing, scratching or scraping. It results in a decrease in the material thickness, which, among other things, reduces its mechanical resistance and protective properties. Abrasion is usually one of the natural results of wear. It may occur locally, and it can also arise quickly if there is accidental contact, such as contact with a moving abrasive object. Certain polymer materials have good resistance to abrasion, mainly PVC, but also polyurethane and neoprene. No glove is completely resistant to abrasion.
Other risks: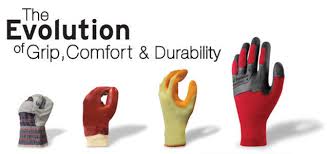
Mechanical risks in work environments are generally present simultaneously with other types of risks. Thus, risk analysis must identify, as precisely and completely as possible, all the risks present. While the focus of interest of the present document is mechanical risks, this section
provides a basic summary of some other types of risks. Indeed, these must be considered in the
glove selection process, not only for their individual effects, but also for their possible influence
on the resistance of gloves to mechanical hazards. If non-mechanical risks are present, one should refer to specialised documentation.
Before purchasing gloves, the PPE Coordinator should review the work activities to determine the degree of dexterity required, the duration, frequency, and degree of exposure to the hazard, and the physical stresses that will be applied. Hand protection must be selected based upon a review of the performance characteristics of the hand protection relative to the task(s) to be performed, conditions present, duration of use, and the existing and potential hazards identified.
There are several factors to consider when selecting a glove, such as size, the type of cuff, lining, and length.
Sizing:
- Gloves come in sizes ranging from small to XX-large. It is important to provide a selection of sizes to employees so that a proper fit is obtained.Gloves that are too small will cause fatigue and gloves that are too large may create dexterity issues, entanglement hazards, or may affect protective qualities.
Cuff type:
- Pinked cuff - A zigzag finished appearance commonly found on knit-lined rubber gloves.
- Rolled cuff - Gives additional cuff strength and a finished appearance. Acts as a barrier to keep chemicals from running off glove onto skin.
- Straight cuff - Provides a snug fit to protect from chemical runoff and skin contact.
- Gauntlet cuff - Extended length protects wrist area. Slides on and off easily. Allows for maximum movement of forearm.
Lining Type:
- Unlined - Gives better sensitivity and dexterity than lined gloves. Required where particle contamination is a concern. Powdered unlined gloves make on/off easier and increase comfort, but may be an irritant to some individual users.
- Flock-lined - Shredded fiber, usually cotton, applied to the inside surface of the glove material. Absorbs perspiration. Easy on/off.
- Knit-lined - Cotton or synthetic material bonded to the inside surface of a glove. Absorbs perspiration, adds some temperature protection.
- Jersey-lined - Softest, most comfortable lining. Gives additional temperature protection and greater cushioning effect.
Length: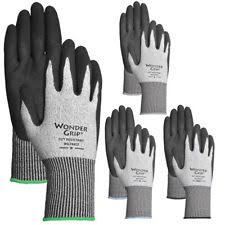
- Finger cots - worn on the fingers alone when minimal or no protection is required.
- 9 - 12 inches provides complete hand protection.
- 12 - 18 inches provides hand, forearm to elbow protection for immersion or extra splash protection.
- 24 - 31 inches provides full arm immersion protection.
Chemical-resistant glove selection begins with an evaluation of the type of work to be performed and the chemical(s) that personnel will be contacting. No glove provides protection against all potential hand hazards, and available gloves may provide only limited protection against many chemicals.It is important, therefore, to select the most appropriate glove for a particular application and to determine how long it can be worn and whether it can be reused. It is often advantageous to select two different types of gloves and wear one pair over the other, thus increasing the range of protection. Chemical-resistant gloves should be inspected prior to use for discoloration, punctures, or tears. Consider the following issues:
The type of chemical(s) to be handled or used:
The frequency and duration of the task for chemical contact. Different chemicals will affect the protective qualities of a glove in different ways.
- Breakthrough time: the time it takes for the chemical to pass to the inside of the glove. Some gloves are not recommended for certain chemicals. Some specified a time limit before chemical breakthrough of the glove material was detected. Some did not detect a breakthrough (under laboratory test conditions). Follow manufacturer guidelines or supplier "Chemical Compatibility Guides" for additional information.
- Permeation: if a chemical will pass through a glove material.
- Degradation: how the chemical will affect the physical properties of the glove material upon contact. Degradation can lead to softening, drying, swelling, shrinkage, or other undesirable side effects that could expose the employee to the chemical.
The ability of the chemical to penetrate through the glove must be determined.
- Latex/natural rubber does not hold up well to organic solvents, oils, greases, or fuels such as kerosene or gasoline.
- Nitrile is ideal for stripping and degreasing, chemical washing, and is resistant to animal fats and vegetable oils. Nitrile does not contain latex that causes skin allergies.
- Polyvinyl chloride (PVC) provides excellent resistance to most acids, fats, and petroleum hydrocarbons.
- Neoprene is strong and durable and provides excellent chemical resistance. Note: Check "Chemical Compatibility Guides" for specific chemical and glove materials recommended.
- Polyvinyl alcohol (PVA) has an extremely high resistance to aliphatics, aromatics, chlorinated solvents, esters, and ketones. PVA quickly breaks down when exposed to water and light alcohols.
- Butyl provides excellent chemical resistance to gases and ketones. It is ideal for handling hazardous materials. Butyl is severely affected by fuels and aliphatic and aromatic hydrocarbon solvents.
- Viton is the most resistant of all, and provides high-temperature, fuel-resistance. Recommended for working with extremely hazardous chemicals, such as carcinogenic or highly toxic chemicals.
- Silver-shield provides excellent chemical resistance and is commonly used for hazardous materials work, or work involving multiple chemical hazards.
The toxic properties of the chemical(s) - in particular, chemicals that can cause local effects on the skin and/or pass through the skin and cause systemic effects warrant a higher level of protection.
Mixtures and formulated products (unless specific test data is available) require that gloves should be selected based on the chemical component with the shortest breakthrough time since it's possible for solvents to carry active ingredients through some glove materials.
Personnel must be able to remove the gloves in such a manner as to prevent skin contamination.
- Determine if the task will involve splash hazards, and ensure that adequate protection is used.
- Consider the concentration of the chemical(s).
- Consider the temperature of the chemical(s).
- Consider abrasion, cut, puncture, tear-resistance, and grip requirements.
- For work involving chemicals where there is a skin absorption hazard, double gloving of the appropriate type may be necessary.
Measurement methods of resistance to mechanical hazards:
Standards exist for measurement methods and classification of performance levels in the case of
cuts, punctures, tearing and abrasion. The present section focuses on tools proposed by the
American and European standards organizations; these are the most relevant tools for gloves sold
in Canada. This section also presents the methods for characterizing mechanical resistance and
the system for classifying the performance levels that was used in the interactive selection tool
for protective gloves against mechanical hazards. Currently, the tool takes into account three
properties: cut, puncture and tear resistance.
Cut resistance:
Standardised methods for cut resistance consider slicing, that is, displacement of a blade parallel to its cutting edge. If the blade is displaced in a direction perpendicular to its cutting axis, it is possible that the materials will behave differently and provide a different degree of protection, as
this configuration has not been examined in the standard measurement methods.
American standards:
The sample to be tested is fastened to a semi-cylindrical metal holder and a rectangular blade is
positioned on the surface of the sample, perpendicular to the holder axis. The blade is displaced
horizontally at constant speed until it has cut through the entire sample. The apparatus measures
the distance travelled by the blade to cut through the sample. These measurements are repeated
for different values of force applied vertically by the blade to the sample. Cut resistance
corresponds to the force required to cut the sample with a 20 mm horizontal displacement of the
blade. The higher the value of this force, the greater the resistance of the material to cuts. One of
the apparatus suggested for measuring cut resistance is a tomodynamometer (TDM).
European standards
The European standard, EN 388, which was adopted in 2004, includes a description of a method
for measuring cut resistance of protective gloves [AFNOR, 2004]. It uses a circular rotary blade
applying a force of 5 Newtons to the sample. Cut resistance is designated by the index I, which is
the ratio between the number of cycles required to cut the material to be tested and that obtained
with the reference material (cotton). The greater the number of cycles, and thus the higher the
value of index I, the greater the resistance of the material to cuts.This technique has short comings due, among other factors, to gradual wear of the circular blade.
Method used in the selection tool:
The method used to determine the cut resistance values of the gloves described in the interactive
selection tool employs a TDM and is based on the American standard ASTM F 1790-05, the version adopted in 2005. The cut-through distance required is measured for three different loads applied to the blade, which moves horizontally at a speed of 150 mm/min. The tests, which are spread over at least three different gloves, are repeated at least five times for each of these forces.
Each test is carried out with a new blade. A narrow strip of aluminium film is placed under the
sample to allow an electrical contact that detects when the blade has cut through the entire thickness of the material.
From the 15 measurements obtained for the cut-through displacement (each of which is based on
the vertical load applied), the best curve fit generated by the test points calculates the rating load
corresponding to a 20 mm cut-through displacement. A check on the validity of this result is then
carried out with a new series of measurements performed with this vertical load.
Puncture resistance:
Standard methods of puncture resistance use probes with varying diameters and geometries.
However, all of these probes have a rounded tip. It is possible that measurements of puncture
resistance carried out with wide-diameter probes having the roundest tips do not behave in the
same way as those with more pointed geometries, such as nails or splinters. In addition, it has
been demonstrated that the resistance of gloves to puncture with medical needles, which have a
sharp edge, is very different from the results of puncture tests carried out according to
standardized methods.
Tear resistance:
Tear resistance is not associated with protection against a specific risk but rather provides information on the mechanical resistance of the glove. Depending on the situation, it may be important to use gloves having a high tear resistance, such as when one seeks to preserve the
physical integrity of the glove; by contrast, one might seek low tear resistance to limit the risk of
catching the hand in moving devices. American standards have no specifications for protective
gloves with regards to tear resistance.
Method used in the selection tool:
The method used by the selection tool to determine tear resistance in gloves is based on the European standard EN 388, the version adopted in 2004. For each glove model, two samples arecut out of different gloves for each of the two directions, longitudinal and transverse. The sample’s two “legs” are fastened between the two jaws of a universal-type testing machine so that the force is applied along the axis of the sample.The displacement occurs at a constant velocity of 100 mm/min. In the case of multi layer samples, each layer is tested individually. For each sample tested (that is, two tested lengthwise and two tested width wise for each layer), one measures the maximum force recorded over the 50 mm of the sample torn. The tear resistance is equal to the minimum value of the maximum forces obtained for the most resistant
glove layer.
Classification of performance levels:
The resistance values of protective gloves subjected to the various mechanical hazards are
distributed amongst several performance levels. This simultaneously allows us to compare gloves with one another and with reference to the hazards from which they must protect the user. The value of the performance level increases with the resistance of the glove: a Level 1 glove has low resistance, while a Level 5 glove has high resistance. In general, gloves with a higher performance level provide greater protection. It should be noted that no glove is completely cut proof, puncture-proof or tear-proof.
American standards:
Levels of protective glove performance against mechanical hazards are described in the American standard ANSI/ISEA 105 [ANSI, 2005]. The most recent version was adopted in 2005.
Cut resistance is based on the version of the ASTM F 1790 standard adopted in 1997. It corresponds to the force deployed over a cut-through distance of 25 mm. Puncture resistance
must be measured according to the version of the EN 388 standard adopted in 2003. It corresponds to the maximum force established using a probe with a conical head of 4.5 mm diameter. For these two properties, and as illustrated in the table below, there are six levels. The higher the level, the greater the resistance of the material will be.
Regarding abrasion resistance, the method is provided by the version of the ASTM D3389 standard adopted in 2005. As illustrated in the table below, seven levels of abrasion resistance have been defined: the higher the level, the greater the resistance of the material. Abrasive wheels corresponding to a force of 500 g must be used for levels 0 to 3, and to a force of 1000 g for levels 4 to 6. The end of a test corresponds to the point just before the film or coating has a hole abraded through it. For woven and knit fabrics, the test ends when the first thread or yarn is broken.
European standards
The European standard for protective gloves uses the performance criteria described in the
European standard, EN 388 [AFNOR, 2004]. The most recent version was adopted in 2004. All the methods employed correspond to those described in the version of the EN 388 standard adopted in 2004. Cut resistance is determined using a circular blade. The result is expressed by the index I, which is equal to the ratio of the number of cycles required to cut the material tested and that required to cut the reference material. The puncture method employs a conical head probe with a diameter of 4.5 mm; the resistance corresponds to the force required to puncture the material. The tear resistance is determined with type T samples. The resistance to abrasion equals the number of cycles completed until a hole appears in the sample. The table below reveals that there are four or five levels, classified according to their characteristics: the higher the level, the
greater the resistance of the material.
Use of performance levels:
The performance levels presented in the previous section constitute a precious tool for comparing various glove models with one another, based on their performance in dealing with various mechanical hazards. Thus, based on the performance levels of gloves already used in a work environment, it is possible to find alternative models of gloves providing the same level of
performance. Should the protection provided by one’s current gloves prove inadequate, it may be
possible to identify higher performance gloves to deal with either type of mechanical hazards.
This system of performance levels can also be used to select the glove models required for existing risks. The assessment must be conducted on a case-by-case basis, and with great care. In
particular, all the factors included in the risk assessment and in the glove selection process should be taken into consideration, as presented in Section 3 of the present document. An approach based on the type and potential seriousness of the wound, as described in Section 3.2 (p. 8), might also provide a basis for determining the performance levels required for the gloves. To be more precise, a low-level hazard such as one associated with a superficial injury will only require a low-level performance glove, i.e. one with a level of at least 1 or 2. For a middle-level risk, in which the potential injuries will require medical procedures (such as stitches) without resulting in a loss of functionality, a glove with a level of at least 3 or 4 should be adequate.
Lastly, in high-risk cases that may result in permanent damage even after reconstructive surgery,
level 5 gloves may prove to be indispensable. While this approach is simple, it may be used for
all types of mechanical hazards. None the less, it must be applied cautiously and take into
consideration all factors present.
Training:
Training should be provided on the appropriate use of gloves and include:-
- Preferred method of glove removal
- Cleaning and maintenance
- How to inspect gloves for wear and tear
Use and maintenance of gloves:
- Before use, inspect gloves (even new ones) for physical damage such as tears or pinholes. A more thorough check can be made by filling the gloves with water and tightly rolling the cuff towards the fingers.
- This will help reveal any pinhole leaks.
- Gloves that are discoloured or stiff may also indicate excessive use or degradation from chemicals.
- Dispose of gloves when they show any sign of deterioration.
- Disposable gloves should be changed often and not re-used.
- Any gloves from which hazardous chemical contamination cannot be removed must be collected as
contaminated waste. Gloves contaminated with bio-hazardous material should be handled as bio-hazardous waste. - Do not wear gloves outside of the laboratory. Gloves should NOT be worn in public corridors, or when touching doorknobs, light switches, telephones, key boards or any shared-use item which will be used by others who are not wearing gloves.
- Always wash hands with soap and water after removing gloves.
- Look for an expiration date on individual packages of gloves.Some gloves, especially lightweight disposables, may be flammable: keep hands well away from flames or other high temperature heat sources.
- Wash reusable gloves appropriately before removing them.(NOTE: some gloves, e.g., leather and polyvinyl alcohol, are water-permeable)
- When removing gloves, do so in a way that avoids skin contact with a possibly contaminated glove exterior.
- When used in a laboratory setting, gloves should be disposed of and replaced when overtly contaminated or when the integrity of the glove is compromised, and removed when work is completed.
- Disposable gloves should never be washed, reused, or used for touching “clean” surfaces (keyboards, telephones, etc.). Used gloves should not be worn outside the laboratory.
Click the below links to know and downloads more about hand protection
Gloves selection -Guideline chart
Power point presentation-Hand safety Part-1
Power point presentation-Hand safety Part-2
13 Tool box talk - Hand protection