Compressed gas cylinder:
What are compressed gases:
Thousands of products are available which contain gases and mixtures of gases stored under pressure in cylinders. Most of these gases are classified as "compressed gases" according to WHMIS 1988 technical criteria. The Controlled Products Regulations contain details of these criteria.
three major groups of compressed gases:
There are three major groups of compressed gases stored in cylinders: liquefied, non-liquefied and dissolved gases. In each case, the pressure of the gas in the cylinder is commonly given in units of kilopascals (kPa) or pounds per square inch gauge (psig).
Gauge pressure = Total gas pressure inside cylinder - atmospheric pressure
Atmospheric pressure is normally about 101.4 kPa (14.7 psi). Note that compressed gas cylinder with a pressure gauge reading of 0 kPa or 0 psig is not really empty. It still contains gas at atmospheric pressure.
Liquefied Gases
Liquefied gases are gases which can become liquids at normal temperatures when they are inside cylinders under pressure. They exist inside the cylinder in a liquid-vapour balance or equilibrium. Initially the cylinder is almost full of liquid, and gas fills the space above the liquid. As gas is removed from the cylinder, enough liquid evaporates to replace it, keeping the pressure in the cylinder constant. Anhydrous ammonia, chlorine, propane, nitrous oxide and carbon dioxide are examples of liquefied gases.
Non-Liquefied Gases
Non-liquefied gases are also known as compressed, pressurized or permanent gases. These gases do not become liquid when they are compressed at normal temperatures, even at very high pressures. Common examples of these are oxygen, nitrogen, helium and argon.
Dissolved Gases
Acetylene is the only common dissolved gas. Acetylene is chemically very unstable. Even at atmospheric pressure, acetylene gas can explode. Nevertheless, acetylene is routinely stored and used safely in cylinders at high pressures (up to 250 psig at 21°C).
This is possible because acetylene cylinders are fully packed with an inert, porous filler. The filler is saturated with acetone or other suitable solvent. When acetylene gas is added to the cylinder, the gas dissolves in the acetone. Acetylene in solution is stable.
Pressure hazards associated with compressed gas cylinders:
All compressed gases are hazardous because of the high pressures inside the cylinders. Gas can be released deliberately by opening the cylinder valve, or accidentally from a broken or leaking valve or from a safety device. Even at a relatively low pressure, gas can flow rapidly from an open or leaking cylinder.
There have been many cases in which damaged cylinders have become uncontrolled rockets or pinwheels and have caused severe injury and damage. This danger has happened when unsecured, uncapped cylinders were knocked over causing the cylinder valve to break and high pressure gas to escape rapidly. Most cylinder valves are designed to break at a point with an opening of about 0.75 cm (0.3 inches). This design limits the rate of gas release and reduces cylinder velocity. This limit may prevent larger, heavier cylinders from "rocketing" although smaller or lighter cylinders might take off.
Poorly controlled release of compressed gas in chemical reaction systems can cause vessels to burst, create leaks in equipment or hoses, or produce runaway reactions.
Fire and explosion hazards associated with compressed gases:
Flammable Gases
Flammable gases, such as acetylene, butane, ethylene, hydrogen, methylamine and vinyl chloride, can burn or explode under certain conditions:
Gas Concentration within the Flammable Range: The concentration of the gas in air (or in contact with an oxidizing gas) must be between its lower flammable limit (LFL) and upper flammable limit (UFL) [sometimes called the lower and upper explosive limits (LEL and UEL)]. For example, the LFL of hydrogen gas in air is 4 percent and its UFL is 75 percent (at atmospheric pressure and temperature). This means that hydrogen can be ignited when its concentration in the air is between 4 and 75 percent. A concentration of hydrogen below 4 percent is too "lean" to burn. Hydrogen gas levels above 75 percent are too "rich" to burn.
The flammable range of a gas includes all of its concentrations in air between the LFL and UFL. The flammable range of any gas is widened in the presence of oxidizing gases such as oxygen or chlorine and by higher temperatures or pressures. For example, the flammable range of hydrogen in oxygen gas is 4 to 85 percent and the flammable range of hydrogen in chlorine gas is 4.1 to 89 percent.
Ignition Source: For a flammable gas within its flammable limits in air (or oxidizing gas) to ignite, an ignition source must be present. There are many possible ignition sources in most workplaces including open flames, sparks and hot surfaces.
The auto-ignition (or ignition) temperature of a gas is the minimum temperature at which the gas self-ignites without any obvious ignition sources. Some gases have very low auto-ignition temperatures. For example, phosphine's auto-ignition temperature of 100°C (212°F) is low enough that it could be ignited by a steam pipe or a lit light bulb. Some compressed gases, such as silane and diborane, are pyrophoric - they can ignite spontaneously in air.
Flash-back can occur with flammable gases. Many flammable compressed gases are heavier than air. If a cylinder leaks in a poorly ventilated area, these gases can settle and collect in sewers, pits, trenches, basements or other low areas. The gas trail can spread far from the cylinder. If the gas trail contacts an ignition source, the fire produced can flash back to the cylinder.
Oxidizing Gases
Oxidizing gases include any gases containing oxygen at higher than atmospheric concentrations (above 23-25 percent), nitrogen oxides, and halogen gases such as chlorine and fluorine. These gases can react rapidly and violently with combustible materials such as the following:
- organic (carbon-containing) substances such as most flammable gases, flammable and combustible liquids, oils, greases, many plastics and fabrics
- finely-divided metals
- other oxidizable substances such as hydrazine, hydrogen, hydrides, sulphur or sulphur compounds, silicon and ammonia or ammonia compounds.
Fires or explosions can result.
The normal oxygen content in air is 21 percent. At slightly higher oxygen concentrations, for example 25 percent, combustible materials, including clothing fabrics, ignite more easily and burn much faster. Fires in atmospheres enriched with oxidizing gases are very hard to extinguish and can spread rapidly.
Dangerously Reactive Gases
Some pure compressed gases are chemically unstable. If exposed to slight temperature or pressure increases, or mechanical shock, they can readily undergo certain types of chemical reactions such as polymerization or decomposition. These reactions may become violent, resulting in fire or explosion. Some dangerously reactive gases have other chemicals, called inhibitors, added to prevent these hazardous reactions.
Common dangerously reactive gases are acetylene, 1,3-butadiene, methyl acetylene, vinyl chloride, tetrafluoroethylene and vinyl fluoride.
Health hazards associated with compressed gases:
Many compressed gases are toxic or very toxic. They could cause various health problems depending on the specific gas, its concentration, the length of exposure and the route of exposure (inhalation, eye or skin contact). Contact between the skin or eye and liquefied gases in liquid form can freeze the tissue and result in a burn-like injury.
the danger of an inert gas:
Inert gases, such as argon, helium, neon and nitrogen, are not toxic and do not burn or explode. Yet they can cause injury or death if they are present in sufficiently high concentrations. They can displace enough air to reduce oxygen levels. If oxygen levels are low enough, people entering the area can lose consciousness or die from asphyxiation. Low oxygen levels can particularly be a problem in poorly ventilated, confined spaces.
Cylinders and fittings:
Compressed gases are stored in heavy-walled metal cylinders designed, produced and tested for use with compressed gases. Cylinders are made in a wide variety of sizes and shapes. They range from small lecture bottles, often used for demonstration purposes, to large cylinders over 3 metres long. Cylinders for transportation must meet CSA standard CAN/CSA-B339 "Cylinders, Spheres and Tubes for the Transportation of Dangerous Goods". This standard covers requirements for the manufacturing, inspection, testing, marking, requalification, reheat treatment, repair, and rebuilding of cylinders, spheres, and tubes (containers) for the transportation of dangerous goods. In addition, it includes the requirements for the qualification of new designs and registration requirements. You should also consult CAN/CSA-B340 "Selection and Use of Cylinders, Spheres, Tubes, and Other Containers for the Transportation of Dangerous Goods, Class 2".
Cylinders that meet these criteria are often referred to as "TC approved" cylinders. Cylinders are permanently marked, typically on the shoulder or the top surface of its neck.
Usually, cylinders must be retested or inspected every five or ten years. The date of each test must be stamped on the cylinder.
Cylinder Valves and Connections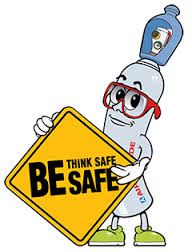
Compressed gas cylinders must be connected only to regulators and equipment designed for the gas in the cylinder. Since connecting the wrong equipment can be dangerous, a number of different standard cylinder valve outlets are available for different classes of gas. For example, these standard connections prevent the valve connection for a flammable gas from fitting the connections for an incompatible gas, such as an oxidizing gas.
Most compressed gas cylinders have valve caps or some other method of protecting the valve from damage during handling and transportation. A dust cap may be placed over the valve outlet itself to help keep it clean.
Cylinder safety devices:
Most cylinders have one or more safety-relief devices. These devices can prevent rupture of the cylinder if internal pressure builds up to levels exceeding design limits. Pressure can become dangerously high if a cylinder is exposed to fire or heat, including high storage temperatures.
There are three types of safety-relief devices. Each relieves excessive gas pressures in a different way:
- Safety- or Pressure-Relief Valves: These valves are usually a part of the cylinder. They are normally held closed by a spring. The force holding the valve closed is set according to the type of gas in the cylinder. The valve opens if the cylinder pressure exceeds the set safety limit. Gas is released until the cylinder pressure drops back to the safety limit. The valve then closes and retains the remaining gas in the cylinder.
- Rupture Discs (also known as frangible or bursting discs): These discs are usually made from metal. They burst or rupture at a certain pressure, releasing the gas in the cylinder. The bursting pressure is designed so that the disc ruptures before the cylinder test pressure is reached. These devices cannot be reclosed, so the entire contents of the cylinder are released.
- Fusible Plugs (also called fuse or melt plugs): Temperature, not pressure, activates fusible plugs. These safety devices are used where heat could initiate an explosive chemical reaction. A pressure-relief valve or rupture disc acts too slowly and too late to prevent rupture of the cylinder if an explosive reaction has already begun. The fusible plug releases the gas before the hazardous reaction can begin. Fusible plugs are made of metals that melt at low temperatures. For example, acetylene cylinders have a fusible plug which melts at about 100°C (212°F). This temperature is safely below the temperature at which hazardous polymerization may occur.
Not all compressed gas cylinders have safety devices. Some gases are so toxic that their release through a safety device would be hazardous. Cylinders for these gases are built to withstand higher pressures than normal cylinders. When these "toxic gas" cylinders are involved in a fire, the area must be evacuated.
Proper ventilation important:
Well-designed and well-maintained ventilation systems remove gases from the workplace and reduce their hazards.
The amount and type of ventilation needed depends on such things as the type of job, the kind and amount of materials used, and the size and layout of the work area.
Assess the specific ways your workplace stores, handles, uses and disposes of its compressed gases. An assessment can reveal if existing ventilation controls and other hazard control methods are adequate. Some workplaces may need a complete system of hoods and ducts to provide acceptable ventilation. Others may require a single, well-placed exhaust fan. Storage facilities for particularly hazardous materials such as chlorine, may require an additional emergency ventilation system, or continuous monitoring with appropriate alarms. Other workplaces using small amounts of inert gases may require no special ventilation system.
Make sure ventilation systems are designed and built so that they do not result in an unintended hazard. Ensure that hoods, ducts, air cleaners and fan are made from materials compatible with the gas used. Systems may require explosion-proof and corrosion-resistant equipment. Separate ventilation systems may be needed for some compressed gases to keep them away from systems exhausting incompatible substances.
Transport or move cylinders:
Always transport cylinders with valve caps or other valve protection in place. Pulling cylinders by their valve caps, rolling them on their sides or dragging or sliding them can cause damage. Rolling cylinders on their bottom edge ("milk churning") may be acceptable for short distances. Never lift cylinders with magnets or chain or wire rope slings. Transport cylinders on specially built hand carts or trolleys or other devices designed for this. All transport devices should have some way of securing cylinders to prevent them from falling.
About the compressed gas storage area:
Store compressed gas cylinders separately, away from processing and handling areas, and from incompatible materials. Separate storage can minimize personal injury and damage in case of fires, spills or leaks. Many compressed gases can undergo dangerous reactions if they come in contact with incompatible materials (gases, liquids or solids), so store them apart from each other. For example, store oxidizing gases at least 6 metres (20 feet) away from fuel gases or other combustible materials, or separate them with an approved fire wall. Check the reactivity information and storage requirements sections of the MSDS for details about which materials are incompatible with a particular compressed gas. The National Fire Code addresses requirements for segregation of different gases in storage.
If compressed gas cylinders are stored outside, use a well-drained, securely fenced area. Keep them on a raised concrete pad or non-combustible rack. Protect cylinders from the weather and do not allow them to stand directly on wet soil as this can cause corrosion.
Indoor storage areas must have walls, floors and fittings made of suitable materials. For example, use non-combustible building materials in storage areas for oxidizing gas and corrosion-resistant materials in storage areas for corrosive gas. Make sure floors are level and protect cylinders from dampness. Avoid overcrowding in storage areas or storing cylinders in out-of-the-way locations.
Always chain or securely restrain cylinders in an upright position to a wall, rack or other solid structure wherever they are stored, handled or used. Securing each cylinder individually is best. Stacking of groups of cylinders together offers some protection, but if this is done improperly, the entire group or individual cylinders could fall.
Store compressed gas cylinders in areas which are:
- Well-ventilated and dry.
- Fire-resistant and supplied with suitable firefighting equipment including sprinklers, where appropriate.
- Away from electrical circuits and ignition sources such as sparks, flames or hot surfaces.
- Accessible at all times, but away from elevators, staircases or main traffic routes where cylinders may be dangerous obstacles.
- Labelled with suitable warning signs.
Always store full cylinders separately from empty cylinders.
compressed gas storage temperatures:
Store compressed gas cylinders in dry, cool areas, out of direct sunlight and away from steam pipes, boilers or other heat sources.
Follow the gas supplier's recommendations for storage and use temperatures. To prevent excessive pressure buildup, never expose cylinders to temperatures above 52°C (125°F). Do not subject them to temperatures below -29°C (-20°F), unless they are designed for this. Cylinders that become frozen to a surface can be freed by using warm water (less than 52°C). Never apply direct heat to a cylinder.
Guidelines for safe handling and use
Use the smallest practical cylinder size for a particular job. Do not keep cylinders longer than the supplier recommends. Compressed gas cylinders are mainly shipping containers. They are built to be as light as possible while remaining safe and durable. Do not drop cylinders or otherwise allow them to strike each other. Rough handling, including using cylinders as hammers or as rollers to move equipment, can seriously damage them.
Do not strike an electric arc on a cylinder. Arc burns can make the metal brittle and weaken the cylinder.
Never tamper with cylinders in any way. Do not repaint them, change markings or identification, or interfere with valve threads or safety devices.
Apart from the fact that it is illegal, it can be dangerous for non-specialists to refill cylinders or to change their contents. Explosions, cylinder contamination or corrosion can result.
Special precautions for oxidizing gases:
Special cleaning procedures (equivalent to oxygen service) are required for all equipment to be used with oxidizing gases. There are several ways to do this. Contact your gas supplier for the best methods for specific systems.
Do not oil or grease any equipment that may contact oxidizing gases. Keep greasy hands, rags and gloves away from any part of the cylinder and fittings. Normal body oils are usually not hazardous, although it is a good practice never to touch any surface that may contact an oxidizing gas. Use lubricants and connection or joint sealants recommended by the gas supplier.
Only use oxygen for its intended purpose. Never use it to purge pipelines or to provide ventilation. Freshening the air with oxygen may make people more comfortable, but it also enriches the oxygen content in the area which can quickly create a major fire hazard. Serious accidents have occurred when oxygen was used to run tools designed for compressed air. High oxygen pressure can cause the lubricant in the tool to explode.
handle and store "empty" cylinders:
Non-Liquefied and Dissolved Gases
The amount of material remaining in a non-liquefied or dissolved gas (acetylene) cylinder is directly proportional to the cylinder pressure gauge reading. As the gas is used, the reading on the cylinder pressure gauge drops. When the cylinder pressure gauge reads zero, the cylinder is not really empty. The cylinder still contains gas at atmospheric pressure. Keep a slight positive pressure in the cylinder. Consider it "empty" when the cylinder pressure gauge reads about 172 kPa (25 psig) or when the cylinder will not deliver at least 172 kPa to the outlet pressure gauge.
Liquefied Gases
The pressure in liquefied gas cylinders remains constant at a given temperature as long as any liquid remains in the cylinder. The only way to know how much material remains in a liquefied gas cylinder is to weigh the cylinder. The empty (tare) weight of the cylinder is stamped on its neck or valve stem. Record the net weight of the cylinder contents on a card attached to it. As with non-liquefied and dissolved gases, never empty the cylinder completely. Keep a small amount of material in the cylinder to maintain a slight positive pressure.
equipment maintenance important:
Regular workplace inspections can help to spot situations where compressed gases are stored, handled, or used in potentially hazardous ways.
Regular inspection of equipment can provide a warning of potential hazards:
- Examine regulators, pressure relief valves and cylinder connections.
- Ensure that cylinders are free of corrosion, leakage, pitting, dents or gouges.
- Regular equipment maintenance can prevent hazardous conditions in the workplace.
Ensure that maintenance personnel:
- Know the possible hazards of the materials they may encounter and any special procedures and precautions before they begin to work.
- Carry out repairs to equipment properly, using equipment suitable for the contents of the compressed gas cylinder.
- Avoid forcing connections, using homemade adaptors or tampering with cylinders in any way.
- Comply with applicable regulations and contact the gas supplier for advice.
What should I do in an emergency:
Act fast in emergencies such as chemical fires or gas cylinder leaks.
- Evacuate the area at once if you are not trained to handle the problem or if it is clearly beyond your control.
- Alert other people in the area to the emergency.
- Call the fire department immediately.
- Report the problem to the people responsible for handling emergencies where you work.
- Obtain first aid and remove all contaminated clothes if you have been exposed to harmful chemicals.
Note: All major compressed gas suppliers have emergency response teams. These teams can be activated by calling the telephone number that is usually printed on the shipping documents and MSDSs.
Locate emergency eyewash stations and safety showers wherever accidental exposure to gases that can damage skin or eyes is possible.
Only specially trained and properly equipped people should handle emergencies. Nobody else should go near the area until it is safe.
Planning, training and practicing for emergencies help people to know what they must do.
The MSDSs for the gases used are a starting point for drawing up an emergency plan. MSDSs have specific sections on spill and leak procedures, first aid instructions, and fire and explosion hazards. If the directions in each MSDS section are not clear or seem incomplete, contact the gas supplier or manufacturer for help. Many other sources can also help develop emergency plans. Local fire departments can assist with fire emergency plans and training. Occupational health and safety and environmental enforcement agencies, provincial safety associations, Compressed Gas Association Inc., St. John Ambulance, insurance carriers, professional societies in occupational health and safety, labour unions, some colleges and universities, and CCOHS can supply useful information. Specialized private consultants are also available.
Basic safe practices when working with compressed gases:
Following these basic general safe practices will help protect you from the hazards of compressed gases:
- Read the MSDSs and labels for all of the materials you work with.
- Know all of the hazards (fire/explosion, health, chemical reactivity, corrosivity, pressure) of the materials you work with.
- Know which of the materials you work with are compressed gases and check the label, not the cylinder colour, to identify the gas.
- Store compressed gas cylinders in cool, dry, well-ventilated areas, away from incompatible materials and ignition sources. Ensure that the storage temperature does not exceed 52°C (125°F).
- Store, handle and use compressed gas cylinders securely fastened in place in the upright position. Never roll, drag, or drop cylinders or permit them to strike each other.
- Move cylinders in handcarts or other devices designed for moving cylinders.
- Leave the cylinder valve protection cap in place until the cylinder is secured and ready for use.
- Discharge compressed gases safely using devices, such as pressure regulators, approved for the particular gas.
- Never force connections or use homemade adaptors.
- Ensure that equipment is compatible with cylinder pressure and contents.
- Carefully check all cylinder-to-equipment connections before use and periodically during use, to be sure they are tight, clean, in good condition and not leaking.
- Carefully open all valves, slowly, pointed away from you and others, using the proper tools.
- Close all valves when cylinders are not in use.
- Never tamper with safety devices in cylinders, valves or equipment.
- Do not allow flames to contact cylinders and do not strike an electric arc on cylinders.
- Always use cylinders in cool well-ventilated areas.
- Handle "empty" cylinders safely: leave a slight positive pressure in them, close cylinder valves, disassemble equipment properly, replace cylinder valve protection caps, mark cylinders "empty" or "MT," and store them separately from full cylinders.
- Wear the proper personal protective equipment for each of the jobs you do.
- Know how to handle emergencies such as fires, leaks or personal injury.
- Follow the health and safety rules that apply to your job.
Click here to download the safety guidelines and check sheet
Compressed gas cylinder safety guidelines
compressed gas cylinder safety check sheet