Arc Flash Safety:
What is an Arc Flash?
An arc flash is a short circuit through air that flashes over from one exposed live conductor to another conductor or to ground.
Simply put, an arc flash is a phenomenon where a flash over of electric current leaves its intended path and travels through the air from one conductor to another, or to ground. The results are often violent and when a human is in close proximity to the arc flash, serious injury and even death can occur.
Arc flash can be caused by many things including:
- Dust
- Dropping tools
- Accidental touching
- Condensation
- Material failure
- Corrosion
- Faulty Installation
- Coming close to a high-amp source with a conductive object can cause the electricity to flash over.
- Dropping a tool or otherwise creating a spark can ignite an arc flash
- Equipment failure due to use of substandard parts, improper installation, or even normal wear and tear
- Breaks or gaps in insulation.
Three factors determine the severity of an arc flash injury:
- Proximity of the worker to the hazard
- Temperature
- Time for circuit to break
Because of the violent nature of an arc flash exposure when an employee is injured, the injury is serious – even resulting in death. It’s not uncommon for an injured employee to never regain their past quality of life. Extended medical care is often required, sometimes costing in excess of $1,000,000.
Definitions
Arc Flash Boundary (ARC) - is the distance at which an electrical arc can flash outward, which may endanger employees working on electrical equipment.
Flash Protection Boundary (FPB) - the calculated safe working distance from electrical equipment which would not expose the employee to the hazards associated with an electrical arc flash.
Electrical Assessment - an analytical evaluation which would calculate the arc flash potential of an electrical component 1 hazard, used to establish the flash protection boundary and the correct level of required PPE, determined by an electrical engineer or the equivalent.
Qualified Employees (per NFPA 70E, 2000 Edition, Standard for Electrical Safety Requirements for Employee Workplaces) - a qualified person shall be trained and knowledgeable of the construction and operation of equipment or a specific work method, and be trained to recognize and avoid the electrical hazards that might be present with respect to that equipment or work method.
Such persons shall also be familiar with the proper use of special precautionary techniques,personal protective equipment, insulating and shielding material!, and insulating tools and test equipment. A person can be considered qualified with respect to certain equipment and methods but still be unqualified for others. Such persons permitted to work within limited approach of exposed energized conductors and circuit parts shall at a minimum, be additionally trained in the following;
- The skills and techniques necessary to distinguish exposed energized parts from other parts of the electric equipment.
- The skills and techniques necessary to determine the nominal voltage of exposed energized parts.
- The approach distance specified in the tables and the corresponding voltage to which the qualified person will be exposed.
- Employees will be capable of reading and understanding the attached PPE matrix, and listed approach boundaries and hazard risk category tables, which are necessary to perform the task safely.
Typical Results from an Arc Flash: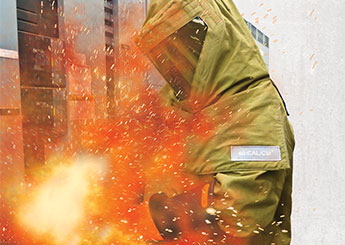
- Burns (Non FR clothing can burn onto skin)
- Fire (could spread rapidly through building)
- Flying objects (often molten metal)
- Blast pressure (upwards of 2,000 lbs. / sq.ft)
- Sound Blast (noise can reach 140 dB – loud as a gun)
- Heat (upwards of 35,000 degrees F)
Current Arc Flash Boundaries:
The arcflash boundaries are designed to keep employees safe while they are working near energized equipment.
- “Prohibited Approach Boundary” removed
- Conductive articles of jewelry and clothing must be removed
- Working space shall not be used for storage
- Barricades shall not be placed closer than the arc flash boundary when it is greater than the limited approach boundary
- Insulated tools must be used when working inside the restricted approach boundary
NFPA 70E 2015 Changes
The NFPA 70E gets updated every three years. The 2015 update includes some of the following changes:
Revision to arc flash warning label content
Elimination of PPE Hazard Category “0”
Elimination of the Prohibited Approach Boundary
Additional boundary requirements
Revisions to selecting appropriate personal protective equipment (PPE)
Updated training and retraining requirements
Minor terminology changes (such as "work shoes" becomes "footwear”)
Flash Protection Boundary (outer boundary):
The flash boundary is the farthest established boundary from the energy source. If an arc flash occurred, this boundary is where an employee would be exposed to a curable second degree burn (1.2 calories/cm2). The issue here is the heat generated from a flash that results in burns.
Limited Approach:
An approach limit at a distance from an exposed live part where a shock hazard exists.
Restricted Approach:
An approach limit at a distance from an exposed live part which there is an increased risk of shock.
Prohibited Approach (inner boundary):
A distance from an exposed part which is considered the same as making contact with the live part.
This distance is not common between equipment. Some equipment will have a greater flash
protection boundary while other equipment will have a lesser boundary.
Ways to Protect the Workers
There exists a number of ways to protect workers from the threat of electrical hazards. Some of the methods are for the protection of qualified employees doing work on electrical circuit and other methods are geared towards non-qualified employees who work nearby energized equipment.
Here are a few of the protective methods:
- De-energize the circuit
- Work Practices
- Insulation
- Guarding
- Barricades
- Ground Fault Circuit Interrupters (GFCI)
- Grounding (secondary protection)
If You Must Work on Energized Circuits
If it has been determined that de-energizing a circuit is not feasible and the employee must work “hot”, the employer shall develop and enforce safety-related work practices to prevent electric shock or other injuries resulting from either direct or indirect electrical contacts.
The specific safety-related work practices shall be consistent with the nature and extent of the
associated electrical hazards.
These safety related work practices could include:
- Energized Electrical Work Permit
- Personal Protective Equipment
- Insulated Tools
- Written Safety Program
- Job Briefing
Additional Boundary Requirements:
Conductive Articles of Jewelry and Clothing - Watchbands, bracelets, rings, key chains, necklaces, metal frame glasses, etc. shall not be worn within the restricted approach boundary.
Working Space - Shall not be used for storage. Space shall be kept clear to permit safe operation and maintenance.
Barricades - When the arc flash boundary is greater than the limited approach boundary, barricades shall not be placed closer than the arc flash boundary.
Insulated Tools - Employees shall use insulated tools when working inside the restricted approach boundary of exposed energized electrical conductors.
Understanding the Arc Flash Warning Labels
Each piece of equipment operating at 50 volts or more and not put into a de-energized state must be evaluated for arc flash and shock protection. This evaluation will determine the actual boundaries (i.e. prohibited, limited, restricted etc) and will inform the employee of what PPE must be worn.
Once the evaluation is complete an Arc Flash Hazard warning label must be affixed to the equipment and readily accessible to employees who may work on the energized equipment.
To increase safety and ensure compliance throughout the workplace, it is essential to identify arc flash hazards in your facilities. Arc flash labeling is an important responsibility that should be addressed by the employer and includes the labeling of electrical equipment, such as switchboards, panel boards, industrial control boards, meter socket enclosures and meter control centers.
These labels should have relevant information to keep employees safe, including nominal system voltage, arc flash boundary and personal protective equipment information.
Minimum arc flash label example
Detailed (preferred) arc flash label example
What Needs to be Labeled?
Arc flash labeling is the responsibility of the employer, not the manufacturer or installer of the equipment. The NEC provides the following examples of electrical equipment that must be field marked with a warning label (This is not an all inclusive list):
- Switchboards
- Panel boards
- Motor control centers
- Industrial control panels
- Meter socket enclosures
Labeling is required for any piece of electrical equipment that is likely to require examination, adjustment, service or maintenance while energized, creating the potential for an arc flash incident to occur. Thus, many employers are also labeling bus ducts and other electrical equipment not specifically called out in the NEC (National Electrical Code).
Any modifications or renovations to electrical equipment that will change data on the label will require an updated arc flash risk assessment and label according to the 2015 NFPA 70E standard. At minimum, the safety program needs to be audited at intervals not to exceed 3 years and arc flash risk assessment shall be periodically reviewed at intervals not to exceed 5 years.
The labeling requirements for equipment installed prior to the 2002 NEC Provision are not specifically stated.
However, OSHA’s general duty clause for hazard warning may apply here. Should the equipment be modified or upgraded in any way, then a label must be affixed. In fact, an OSHA representative has stated that even changing a fuse or circuit breaker could be considered a modification that would require labeling. Labels applied prior to September 30, 2011 are acceptable if they contain the available incident energy or required level of PPE.
From a safety perspective, the hazard is the same regardless of when the equipment was installed. Consequently, most employers are simply labeling all the appropriate equipment, regardless of when it was installed.
The NEC requirement states that the marking must be in a location that is clearly visible to qualified persons before they begin work. Typically, the label is placed outside the panel or enclosure door. In some cases,companies choose to put the label inside the door to protect it from harsh environments; however, this should only be done if the door must be opened (allowing the label to be seen) in order to remove the panel face or enclosure. The key point is that the label should be easily noticeable by workers before they may be exposed to any potentially dangerous live parts.
What Needs to Appear on the Label?
Neither the NFPA 70E nor the NEC requirements specify whether to use a “Danger” or “Warning” header; however, NFPA 70E does recommend identifying those situations in which there is a hazard to the worker. A commonly used guideline is to use a red “Danger” header when the voltage is over 600 volts or when the incident energy is over 40 cals/cm2. Many employers have also
standardized to using the “Danger” signal word to indicate a situation where serious injury or death WILL occur. If it is less than that threshold, an orange “Warning” header is used. The employer has the final decision on which words appear on the labels, but it is imperative that consistency be maintained on all the labels throughout the facility.
It is also important to note that arc flash labels must be able to withstand their usage environment. This means that the print should not fade and the adhesive should be aggressive enough to avoid peeling. When necessary, an over laminate should be applied to protect the printed surface from harsh chemicals and exposure to sunlight.
How Many Labels per equipment?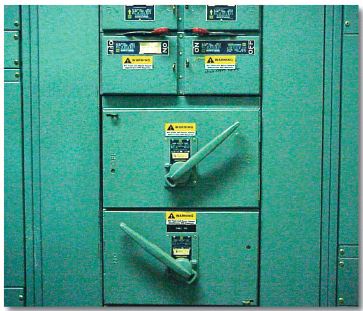
A frequently asked question is how many labels are enough? Obviously if one is good, more is better – right? This philosophy has both positive and negative aspects that must be considered. The more labels used the higher the visibility factor. However, too many labels clutter the objective and cause workers to ignore the warning.
For the MCC above, a simple one-word “warning” label was used without providing specific PPE, boundary information, or hazard levels. This minimizes clutter, however, if you take a step back and see 50-75 of these labels the clutter becomes obvious. The clutter is even more prevalent and confusing if the standard AFH information is included on the labels. The worker looking at the MCC must then determine
1) Which label is important?
2) If the labels are different, what information applies to this task?
3) How do I react to these circumstances?
Examples
This section provides multiple labeling examples for different types of electrical equipment, which can be modified or extrapolated to fit your system. For some equipment types, multiple options will be provided.
Panels
Panels are typically of box construction with a fixed backing plate attached to a beam/ wall mounted. The front of the panel, which provides opening access, is bolted in place. The front cover typically has a hinged opening, which allows viewing and operation of the breakers. For standard 42 circuit
lighting panels, the typical labeling procedure is one label on the main cover, top center. See Figure-1.
Panel boards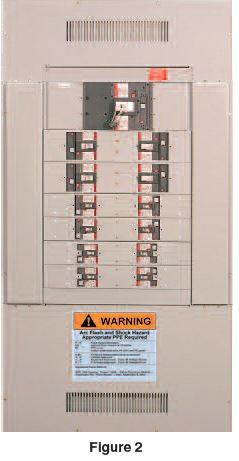
Panel boards, sometimes called distribution panel boards (DPB), or distribution boards are larger than a standard panel and may range from 400-1200A. They are typically standalone, but smaller units may be wall or beam mounted. Larger units may be accessible front and back side via bolted covers. For standard DPB’s, typical labeling procedures is one label on the main cover, top center. For the example shown in Figure-2, the label was moved to the bottom to prevent covering the cooling vents. Panel boards, do not have isolated and barrier protected main breakers unless specially ordered and should always have only one label.
Dry Type Transformers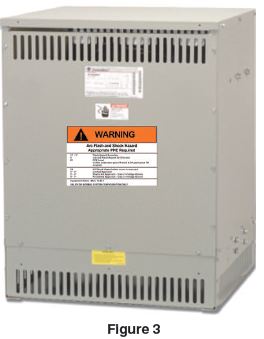
Dry type transformers typically have a bolted on face plate section with exposed terminals behind the face plate. Since this is the main access point, it is usually not necessary to label the other sides.Figure-3
Variable Frequency Drives,and Control Cabinets
Variable frequency drives and control cabinets are typically hinged front opening units with an open, exposed incoming main breaker. The incoming breaker or fuse is typically not isolated or barrier protected from the other sections and therefore cannot be used for AFH protection. Like other cabinets, one “worst case” label is typically sufficient. See Figure-4.
Switchboards and Switch gear
Switchboards and Switch gear are the standard for low voltage distribution equipment. Switch gear by definition has isolated and barrier protected cubicles, rack-in air frame breakers/switches, and isolated bus. Switchboards may have similar attributes but will most likely be equipped with molded case or insulated case breakers, or fuses in non-isolated cubicles with non-isolated bus work. By special order, the main breaker/switch can be isolated, enhancing arc flash protection.For a typical 4 section or less switch gear lineup, only one label (worst case) on the front side is
necessary. For longer sections additional labels can be applied every 5-10 feet. Since both front and back-side switch gear covers are hinged, the back-side covers should also be labeled.
For switchboards, the back-sides are typically open exposed bus with bolted covers, which should prevent access. Labeling should be optional since access is not easily obtained.
Do’s and Don’ts of AFH labeling:
Do’s
- Do label “WORST” case energy or PPE level. Consider all possible modes of operation.
- Do label per ANSI Z535.4
- Do label using only one color, Orange for Warning or Red for Danger.
- Do standardize on only one working distance – preferably 18 inches for all labels in a facility.
- Manage down PPE levels using work permits stating increased distances based on work task and proper safety procedures.
- Label to warn of potential danger, not for the purpose of working on the equipment.
- Do use common sense in your hazard labeling.
- Do implement NFPA 70E Article 130.1 work permit requirements for all energized work even if a label is present.
Don’ts
- Do not label each MCC bucket, breaker/fuse cubicle, or plug-in (busway).
- Do not label using colors for PPE level.
- Don’t label with multiple distances or PPE levels on the same equipment.
- Don’t make it complicated.
- Don’t substitute labeling for NFPA 70E Article 130.1 work permit requirements.
Personal and Other Protective Equipment:
A. General
Employees working in areas where electrical hazards are present shall be provided with, and shall use, protective equipment that is designed and constructed for the specific part of the body to be protected and for the work to be performed.
B. Care of Equipment
Protective equipment shall be maintained is a safe, reliable condition. The protective equipment shall be visually inspected before each use.
C. Personal Protective Equipment
1. General
When an employee is working within the Flash Protection Boundary he/she shall wear protective clothing and other personal protective equipment in accordance with NFPA 70E.
2. Movement and Visibility
When flame-resistant (FR) clothing is worn to protect an employee,it shall cover all ignitable clothing and shall allow for movement and visibility.
3. Head, Face, Neck, and Chin Protection
Employees shall wear non-conductive head protection wherever there is a danger of head injury from electric shock or burns due to contact with live parts or from flying objects resulting from electrical explosion. Employees shall wear non-conductive protective equipment for the face, neck, and chin whenever there is a danger of injury from exposure to electric arcs of flashes or from flying objects resulting from electrical explosion.
4. Eye Protection
Employees shall wear protective equipment for the eyes whenever there is danger of injury from electric arcs, flashes, or from flying objects resulting from electrical explosion.
5. Body Protection
Employees shall wear FR clothing wherever there is possible exposure to an electric arc flash above the threshold incident-energy level for a second-degree burn. 5 J/cm2 (1.2 cal/cm2). Such clothing can be provided as shirt and trousers, or as coveralls, or as a combination of jacket and trousers, or, for increased protection, as coveralls with jacket and trousers. Various weight fabrics are available. Generally, the higher degree of protection is provided by heavier weight fabrics and/or by layering combinations of one or more layers of FR clothing. In some cases one or more layers of FR clothing are worn over flammable, non melting clothing. Non-melting, flammable, clothing, used alone, can provide protection at low incident energy levels of 8.36 J/cm2 (2.0 cal/cm2) and below.
6. Hand and Arm Protection
Employees shall wear rubber insulating gloves where there is danger of hand and arm injury from electric shock due to contact with live parts. Hand and arm protection shall be worn where there is possible exposure to arc flash burn.
7. Foot and Leg Protector
Where insulated footwear is used as protection against step and touch potential,dielectric overshoes shall be required. Insulated soles shall not be used as primary electrical protection.
8. Selection of Personal Protective Equipment
When Required for Various Tasks When selected in lieu of the flash hazard analysis, NFPD table
130.7(C)(9)(a) shall be used to determine the hazard risk category for a task. The assumed short-circuit current capacities and fault clearing times for various tasks. Systems with greater than the assumed fault clearing times, a flash hazard analysis shall be required.
Both larger and smaller available short-circuit currents could result in higher available arc-flash energies. If the available short circuit current increases without a decrease in the opening time of
the over current protective device, the arc-flash energy will increase. If the available short-circuit current decreases, resulting in a longer opening time for the over current protective device, arc flash
energies could also increase.
Factors in Selection of Protective Clothing
Clothing and equipment that provide worker protection from shock and arc flash hazards shall be utilized. Clothing and equipment required for the degree of exposure shall be permitted to be worn alone or integrated with flammable , non melting apparel. If FR clothing is required, it shall cover associated parts of the body as well a all flammable apparel while allowing movement and visibility.
All personal protective equipment shall be maintained is a sanitary and functionally effective condition. Personal protective equipment items will normally be used in conjunction with one another as a system to provide the appropriate level of protection.
Layering
Non melting, flammable fiber garments shall be permitted to be used as under layers in conjunction with FR garments in a layered system for added protection. If non melting, flammable fiber
garments ate used as under layers the system arc rating shall be sufficient to prevent break open of the innermost FR layer at the expected arc exposure incident energy level to prevent ignition of flammable under layers. A typical layering system might include cotton shirt and trouser, and a FR coverall. Specific tasks might call for additional FR layers to achieve the required protection level.
Outer Layers
Garments worn as outer layers over FR clothing, such as jackets or rain wear, shall also be made from FR material.
Under layers
Melt able fibers such as acetate, nylon, polyester, polypropylene, and spandex shall not be permitted. in fabric under layers (underwear) next to the skin.
Coverage
Clothing shall cover potentially exposed areas as completely as possible. Shirt sleeves shall be fastened at the wrist, and shirts and jackets shall be closed at the neck.
Fit
Tight-fitting clothing shall be avoided. Loose fitting clothing provides additional thermal insulation because of sir spaces. FR apparel shall fit properly such that it does not interfere with the work task.
Interference
The garment selected shall result in the least interference with the task but still provide the necessary protection. The work method,location, and task could influence the protective equipment
selected.
Click the below link to download the guidelines,PPT and safety check sheet
Safety Guideline - Arc Flash safety
Power point Presentation - Arc Flash safety-1
Power point Presentation - Arc Flash safety-2
Safety Check list - Arc Flash safety
Arc Flash Safety Training Video
Arc Flash PPE Laboratory Test Video