Sling:
INTRODUCTION:
What is the purpose of this guide?
The purpose of this guide is to assist employers and employees in the proper selection, use, and maintenance of slings and in the recognition of hazards associated with their use. This guide is designed to assist you in understanding and complying with OSHA's standards for sling use in General Industry, Maritime, and Construction.
You should also be aware that there are certain States (OSHA-approved State Plans) which operate their own programs under agreement with the U.S. Department of Labor, pursuant to section 18 of the OSH Act. These programs may differ in some details from the Federal OSHA program.
Why is this guide important?
From time to time almost all employees are involved in moving materials, structures or products; these activities often lead to injuries, which in many instances can be avoided by using safe materials handling practices. To avoid sprains, strains, muscle pulls or more severe injuries including death, whenever possible, ensure that mechanical means are used to move heavy, bulky objects.
Equipment such as powered industrial trucks, cranes, hoists, and derricks are used to aid in the movement of materials (especially large, bulky, or heavy loads). These types of equipment use slings to hold their suspended loads. This guide will offer information on the proper selection, use, and maintenance of slings.
Who should read this guide?
The handling of materials and finished products is key to the successful operation of many industries, which use, manufacture, construct, and sell materials, structures, or products. Anyone (including employers, employees, safety professionals, and engineers) responsible for handling of or moving materials and finished products from one location to another should read this guide. This guide can help you identify and manage the hazards associated with sling use.
What type of hazards should I look for?
This guide will help employers and employees recognize hazardous conditions, such as:
- Improper sling or attachments for the type of load to be lifted and the environment in which it is being lifted;
- Worn slings and attachments or those with damage such as cracks, kinks, bends, cuts, gouges, and frayed fibers; and
- Improper storage of slings and misuses such as resting of loads on the sling or dragging of slings across abrasive floors.
This guide will also help employers and employees identify and avoid hazardous work practices, such as:
- Riding slings or walking under suspended loads; and
- Using improperly repaired or reconditioned slings and attachments or slings and attachments that must be removed from service.
TYPES OF SLINGS:
This section describes several types of slings and provides specific information for their proper selection, use, and maintenance. This guidance document is not an attempt to explain OSHA's sling standard requirements. It is advisory in nature and informational in content and its recommendations on safe practices should help reduce and prevent injuries and fatalities related to improper sling use. It also discusses slings which are currently in use that are not covered in OSHA's standard.
There are several varieties of slings, including: alloy steel chain, wire rope, metal mesh, natural fiber rope, synthetic fiber rope, synthetic web, and synthetic round slings. Each type of sling has its advantages and disadvantages.
Many factors come into play when choosing the best sling for the task at hand. These include size, strength, flexibility, and weight, as well as suitability for the work environment, shapes of the load, and environmental conditions in which the sling will be used. Below are links to the six types of slings. Click on a link to view information on that type of sling.
- Alloy Steel Chain Slings(Below in details)
- Wire Rope Slings
- Metal Mesh Slings
- Natural and Synthetic Fiber Rope Slings
- Synthetic Web Slings
- Synthetic Round Slings
Alloy Steel Chain Slings:
Alloy steel chains are often used because of their strength, durability, abrasion resistance and ability to conform to the shape of the loads on which they are used. In addition, these slings are able to lift hot materials.
Alloy steel chain slings are made from various grades of alloy, but the most common grades in use are grades 80 and 100. These chains are manufactured and tested in accordance with ASTM (American Society for Testing and Materials) guidelines. If other grades of chain are used, use them in accordance with the manufacturer's recommendations and guidance.
Identification: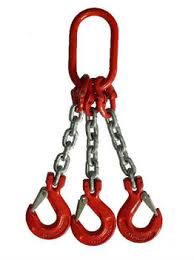
New slings are marked by the manufacture to show:
- Size,
- Grade,
- The rated load, and
- Length (reach).
In addition, slings may be marked to show:
- Number of legs,
- Individual sling identification (i.e., serial number), and
- The name or trademark of the manufacturer.
Rated Loads:
Rated loads (capacities) for single-, double-, triple- and quadruple-leg slings and single- and double-basket slings used in vertical, bridle, or basket hitches are given in Tables 1 and 2 for the horizontal angles listed.
TABLE 1
RATED LOAD FOR GRADE 80 ALLOY STEEL CHAIN SLINGS
VERTICAL AND BRIDLE HITCHES
NOTES:
(1) The horizontal angle is the angle formed between the inclined leg and the horizontal plane [see figure 1(d)].
TABLE 2
RATED LOAD FOR GRADE 100 ALLOY STEEL CHAIN SLINGS
VERTICAL AND BRIDLE HITCHES
For angles not shown, use the next lower angle or have a qualified person calculate the rated load for the new angle. Rated loads are based on:
- Material strength,
- Design factor,
- Type of hitch,
- Angle of loading,
Do not use horizontal angles less than 30 degrees except as recommended by the sling manufacturer or a qualified person.
Rated loads for single-, double-, triple-, and quadruple-leg slings used in a choker hitch are given in Tables 3 and 4 for the horizontal angles listed provided that the angle of choke is greater than 120 degrees (see Fig.1). For angles of choke less than 120 degrees, use the rated loads provided by the sling manufacturer or a qualified person.
For other materials and for configurations not shown, use the rated loads according to the sling manufacturer or a qualified person.
Attachments:
Use attachments, such as hooks, rings, oblong links, pear-shaped links, or welded or mechanical coupling links that have a rated capacity at least equal to that of the alloy steel chain with which they are used. If attachments with rated capacities lower than the chain are used, ensure that the sling is rated to the weakest component used on the sling.
TABLE 3
RATED LOAD FOR GRADE 80 ALLOY STEEL CHAIN SLINGS
CHOKER HITCHES [Note 2]
Fig. 1 Alloy Steel Chain Slings: Configurations, Components, and Hitches
TABLE 4
RATED LOAD FOR GRADE 100 ALLOY STEEL CHAIN SLINGS
CHOKER HITCHES [Note2]
For other materials and for configurations not shown, use the rated loads according to the sling manufacturer or a qualified person.
Attachments:
Use attachments, such as hooks, rings, oblong links, pear-shaped links, or welded or mechanical coupling links that have a rated capacity at least equal to that of the alloy steel chain with which they are used. If attachments with rated capacities lower than the chain are used, ensure that the sling is rated to the weakest component used on the sling.
Inspections:
Designate a qualified person to inspect slings and all fastenings and attachments each day before use for damage or defects.
This qualified person also performs additional periodic inspections where service conditions warrant, as determined on the basis of:
Qualified person: A person who, by possession of a recognized degree or certificate of professional standing in an applicable field, or who, by extensive knowledge, training, and experience, has successfully demonstrated the ability to solve or resolve problems relating to the subject matter and work.
- Frequency of sling use,
- Severity of service conditions,
- Nature of the lifts being made, and
- Experience gained during the service life of slings used in similar circumstances.
Make periodic inspections of alloy steel chains slings at intervals no greater than 12 months. A good guide to follow includes:
- Yearly for normal service use,
- Monthly to quarterly for severe service use, and
- As recommended by a qualified person for special and infrequent service use.
Develop a system to make sure that these inspections are conducted. To do this, you can use a record keeping system, such as logs or marking the inspection date on a tag attached to the sling.
Make a thorough inspection of slings and attachments. Items to look for include:
- Wear;
- Defective welds.
- Nicks, cracks, breaks, gouges, stretch, bends, discoloration due to excessive heat,
- Excessive pitting or corrosion,
- Throat opening of hooks,
- Missing or illegible sling identifications, and
- Other conditions that cause doubt as to continued safe use of the sling.
Where any such defect or deterioration is present, remove the sling or attachment from service immediately.
Repairing/Reconditioning:
Do not use worn or damaged alloy steel chain slings or attachments. Discard or repair them. Use damaged slings only after they are repaired, reconditioned, and proof tested by the sling manufacturer or a qualified person using the following criteria:
- Ensure that slings and attachments conform to the original strength requirements,
- Mark those slings or attachments to identify who made the repairs,
- Replace rather than repair cracked, broken, or bent links, and
- Do not use mechanical coupling links or carbon steel repair links to repair broken lengths of alloy chain.
Operating practices:
Do not use alloy steel slings with loads exceeding the rated loads (capacities) described in Tables 1 and 3 for grade 80 or Tables 2 and 4 for grade 100. Ensure that alloy steel chain slings not included in these tables are used only in accordance with the manufacturer's recommendations. Follow other safe operating practices, including:
Sling Selection
- For multiple-leg slings used with non symmetrical loads, ensure that an analysis by a qualified person is performed to prevent overloading of any leg,
- Ensure that multiple-leg slings are selected according to Table 1 or 2 when used at the specific angles given in the tables. Ensure that operations at other angles are limited to the rated load of the next lower angle given in the tables or calculated by a qualified person, and
- Do not use a component unless it is the proper shape and size to ensure that it is properly seated in the hook or lifting device.
Cautions to Personnel
- Ensure that all portions of the human body are kept away from the areas between the sling and the load and between the sling and the crane or hoist hook,
- Ensure that personnel never stand in line with or next to the legs of a sling that is under tension,
- Ensure that personnel do not stand or pass under a suspended load, and
- Ensure that personnel do not ride the sling or the load, unless the load is specifically designed and tested for carrying personnel.
Effects of Environment: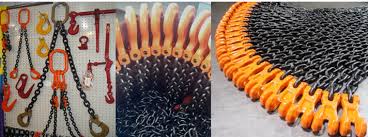
- Store slings in an area where they will not be subjected to mechanical damage, corrosive action, moisture, extreme temperatures, or to kinking, and
- When slings are exposed to extreme temperatures, follow the guidance provided by the sling manufacturer or qualified person.
Rigging Practices:
- Ensure that slings are hitched in a manner providing control of the load,
- Ensure that sharp edges in contact with slings are padded with material of sufficient strength to protect the sling,
- Ensure that slings are shortened or adjusted only by methods approved by the sling manufacturer or a qualified person,
- Ensure that, during lifting with or without a load, personnel are alert for possible snagging,
- Ensure that, in a basket hitch, the load is balanced to prevent slippage,
- When using a basket hitch, ensure that the legs of the sling contain or support the load from the sides, above the center of gravity, so that the load remains under control,
- Ensure that, in a choker hitch, the choke point is only on the sling body, never on a fitting,
- Ensure that, in a choker hitch, an angle of choke less than 120 degrees is not used without reducing the rated load,
- Ensure that slings are not constricted, bunched, or pinched by the load, hook, or any fitting,
- Ensure that the load applied to the hook is centered in the base (bowl) of the hook to prevent point loading on the hook, unless the hook is designed for point loading,
- Do not shorten or lengthen a sling by knotting or twisting,\
- Do not rest loads on the sling,
- Do not pull a sling from under a load when the load is resting on the sling,
- Do not drag slings on the floor or over abrasive surfaces,
- Do not allow shock loading, and
- Avoid twisting and kinking.
Proof testing:
Before initial use of a sling, ensure that every component of a new, repaired, or reconditioned alloy steel chain sling has been proof tested by the sling manufacturer or a qualified person and meets the requirements of the American Society of Testing and Materials Specification A906-02.
Retain the certificates of proof test and make them available for examination.
Environmental Effects:
Do not use alloy steel chains that have been heated above 1,000 degrees F (538 degrees C). Remove them from service.
Alloy chain slings exposed to temperatures above 400 degrees F (205 degrees C) have reduced load ratings. Reductions in rated load for Grade 80 and Grade 100 chain slings used at and after exposure to elevated temperatures are given in Table 5.
If chain slings are to be used at temperatures below minus 40 degrees F (minus 40 degrees C), consult the chain manufacturer.
The strength of alloy steel chain slings can be affected by chemically active environments. Consult the manufacturer before the sling is to be used in chemically active environments.
Click the below link to download the OSHA standard safety sheet
Sling - General requirement safety check sheet
Sling - Steel Chain, Wire Rope, and Metal Mesh safety check sheet
Sling - Natural Rope, Synthetic Rope, and Synthetic Web safety check sheet